Motor operation control method based on discrete current vector phase-amplitude coordination
A discrete current, coordinated control technology, used in motor generator control, electronic commutation motor control, vector control systems, etc., can solve problems such as low positioning accuracy, excessive torque ripple, and long positioning time.
- Summary
- Abstract
- Description
- Claims
- Application Information
AI Technical Summary
Problems solved by technology
Method used
Image
Examples
Embodiment
[0106] In this embodiment, the operation process of a 2.2kW permanent magnet synchronous motor is taken as an example, the load is set as an impedance load, the large inertia load torque is 2N m, and the moment of inertia is 0.089kg m 2 , the maximum speed is limited to 1000r / min, the given positioning position is 200rad, and the discrete number b is taken H = 12, the whole operation process is divided into four stages, namely, the speed-up stage ①, the constant speed stage ②, the deceleration stage ③, and the positioning stage ④. The whole running time is 2.6s. by such as Figure 6 , Figure 7 The motor speed curve, position curve, electromagnetic torque curve, current vector amplitude curve and torque angle curve at each stage of the whole operation process are shown. In addition, the phase-amplitude coordinated control method based on discrete current vectors in the present invention is also applicable to other types of motors such as asynchronous motors and switched relu...
PUM
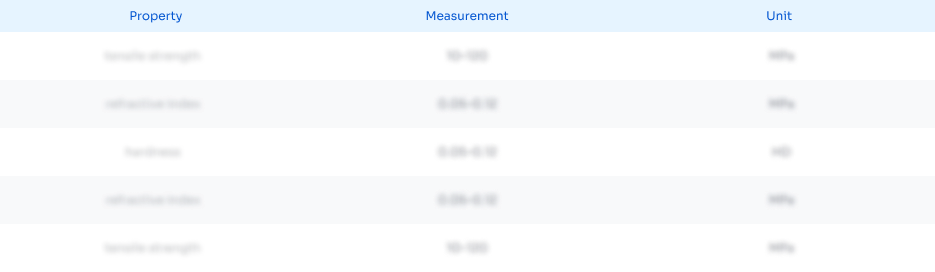
Abstract
Description
Claims
Application Information

- R&D
- Intellectual Property
- Life Sciences
- Materials
- Tech Scout
- Unparalleled Data Quality
- Higher Quality Content
- 60% Fewer Hallucinations
Browse by: Latest US Patents, China's latest patents, Technical Efficacy Thesaurus, Application Domain, Technology Topic, Popular Technical Reports.
© 2025 PatSnap. All rights reserved.Legal|Privacy policy|Modern Slavery Act Transparency Statement|Sitemap|About US| Contact US: help@patsnap.com