Special organic silicon defoamer for textile industry
An organosilicon defoamer, a technology of the textile industry, applied in textiles, papermaking, fiber treatment, etc., can solve problems such as economic loss, loss of working fluid, product downgrade, etc., achieve chemical stability, good antifoam performance, and The effect of heat resistance
- Summary
- Abstract
- Description
- Claims
- Application Information
AI Technical Summary
Problems solved by technology
Method used
Examples
Embodiment 1
[0008] A special organosilicon defoamer for the textile industry, which is made of the following raw materials in parts by weight:
[0009] 3 parts of petroleum sulfonic acid, 2 parts of hexamethylenetetramine, 5 parts of dialdehyde starch, 8 parts of polyvinyl acetate, 12 parts of white carbon black, 5 parts of polyether modified silicone, sorbitan fatty acid 3 parts of ester, 2 parts of thiobisethyl alcohol, 4 parts of thiourea dioxide, 5 parts of sodium dithionite, 8 parts of thickener, 4 parts of low hydrogen silicone oil, 2 parts of hydroxyl-terminated polydimethylsiloxane, aluminum oxide 4 parts, sodium chloride 2 parts.
Embodiment 2
[0011] A special organosilicon defoamer for the textile industry, which is made of the following raw materials in parts by weight:
[0012] 5 parts of petroleum sulfonic acid, 4 parts of hexamethylenetetramine, 17 parts of dialdehyde starch, 16 parts of polyvinyl acetate, 22 parts of white carbon black, 7 parts of polyether modified silicone, sorbitan fatty acid 5 parts of ester, 6 parts of thiobisethyl alcohol, 7 parts of thiourea dioxide, 8 parts of sodium dithionite, 14 parts of thickener, 7 parts of low-hydrogen silicone oil, 5 parts of hydroxyl-terminated polydimethylsiloxane, aluminum oxide 7 parts, sodium chloride 4 parts.
PUM
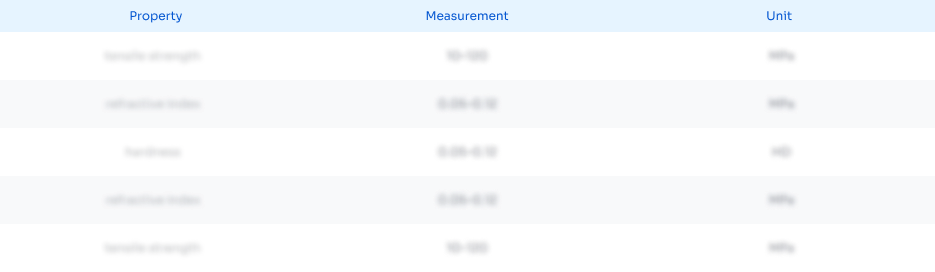
Abstract
Description
Claims
Application Information

- R&D
- Intellectual Property
- Life Sciences
- Materials
- Tech Scout
- Unparalleled Data Quality
- Higher Quality Content
- 60% Fewer Hallucinations
Browse by: Latest US Patents, China's latest patents, Technical Efficacy Thesaurus, Application Domain, Technology Topic, Popular Technical Reports.
© 2025 PatSnap. All rights reserved.Legal|Privacy policy|Modern Slavery Act Transparency Statement|Sitemap|About US| Contact US: help@patsnap.com