Powdered rubber isolating agent
A powder rubber and release agent technology, applied in the chemical field, can solve the problems of uneven quality, affecting the performance of the rubber compound, white powder pollution, etc., and achieve the effect of no impact on the performance of the rubber compound, excellent isolation effect, and not easy to precipitate
- Summary
- Abstract
- Description
- Claims
- Application Information
AI Technical Summary
Problems solved by technology
Method used
Image
Examples
Embodiment 1
[0024] The composition of embodiment 1 powder rubber release agent
[0025] The composition of the powder rubber release agent of the present invention is respectively numbered 1-5, as shown in Table 1
[0026] Table 1 Composition of powder rubber release agent
[0027] material name 1 2 3 4 5 Clay 70 80 90 60 100 Nano calcium carbonate 25 15 5 10 5 DP270 1 1 1 1 1 mineral oil 2 2 2 2 2 Zinc stearate 2 2 2 2 2
[0028] Among them, inorganic mineral clay can be replaced by talcum powder, clay, kaolin or mica powder or a combination thereof; defoamer can be replaced by AF-9020, Foamkill 800 Series or 8 Series; fatty acid zinc stearate can be Use sodium stearate instead.
Embodiment 2
[0029] The preparation method of embodiment 2 powder rubber release agent
[0030] After weighing clay, nano-calcium carbonate and zinc stearate, add them to the high-speed mixer at a speed of 1400rpm, and stir for 3 minutes. Then weigh the liquid materials DP270 and mineral oil and add them into the high-speed mixer slowly at a uniform speed. The feeding time of the material is controlled at more than 7 minutes. After the liquid material is added, the stirring is continued for 5 minutes, and the material is discharged to obtain the powdered rubber release agent.
[0031] According to the preparation method of the powder rubber release agent, the number 1-5 powder rubber release agent was prepared according to the components of the number 1-5 in Example 1 respectively.
Embodiment 3
[0032] Embodiment 3 preparation is used for the film of performance test and isolation effect test
[0033] Preparation method of film for performance test and isolation effect test
[0034] 1. Take 50 grams of powdered rubber release agent samples, disperse them in 2000 grams of water, stir them evenly, and make a release agent water solution with a concentration of 2.5%;
[0035] 2. Film preparation: Weigh the following sizing materials in parts by weight: 100 parts of natural rubber (NR); 40 parts of carbon black; 5 parts of softening oil; 5 parts of zinc oxide; 2 parts of stearic acid; 5 parts of antioxidant; 1.5 parts of sulfur parts; accelerator 1.2 parts, knead into a film with a thickness of about 5mm in an open mill.
[0036] 3. The blank film is the film made in the above step 2, and the surface does not contain any release agent;
[0037] The films made in the above step 2 were respectively immersed in the water solution of the release agent No. 1-5 in the embodim...
PUM
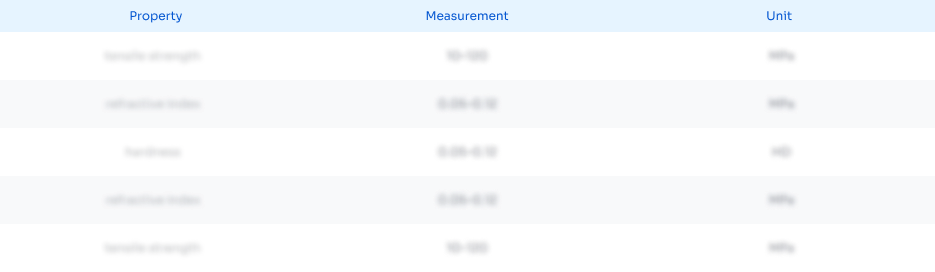
Abstract
Description
Claims
Application Information

- Generate Ideas
- Intellectual Property
- Life Sciences
- Materials
- Tech Scout
- Unparalleled Data Quality
- Higher Quality Content
- 60% Fewer Hallucinations
Browse by: Latest US Patents, China's latest patents, Technical Efficacy Thesaurus, Application Domain, Technology Topic, Popular Technical Reports.
© 2025 PatSnap. All rights reserved.Legal|Privacy policy|Modern Slavery Act Transparency Statement|Sitemap|About US| Contact US: help@patsnap.com