Production method for reducing pinhole short circuit through photoresist insulation according to BM technology
A production method and photoresist technology, applied in the post-processing of printing, printing, printing devices, etc., can solve the problems of waste of materials, low production line efficiency, and consumption of screen printing machine equipment, so as to solve the problem of short circuit and reduce labor cost, increase production efficiency and the effect of yield rate
- Summary
- Abstract
- Description
- Claims
- Application Information
AI Technical Summary
Problems solved by technology
Method used
Examples
Embodiment Construction
[0018] A manufacturing method for photoresist insulation in BM process to reduce pinhole short circuit, including the following steps:
[0019] (1) Use the existing conventional yellow light process to make the ITO pattern of the OGS touch screen on the glass substrate first, and wait for the BM silk screen;
[0020] (2) Scrape the silk screen BM with the squeegee screen printing process, and put it into the oven for baking after completion, the temperature is 200-230℃, and the time is 40-45 minutes;
[0021] (3) Silk-print a negative photoresist insulating layer on the BM, put it into the oven for baking after completion, the temperature is 160-180℃, and the time is 25-30 minutes;
[0022] (4) Silk-screen via hole carbon paste, put it into the oven for baking after completion, the temperature is 160-180℃, and the time is 25-30 minutes;
[0023] (5) The silver paste is exposed by silk-screening under yellow light. After the silk-screening is completed, it is put into the oven for baking...
PUM
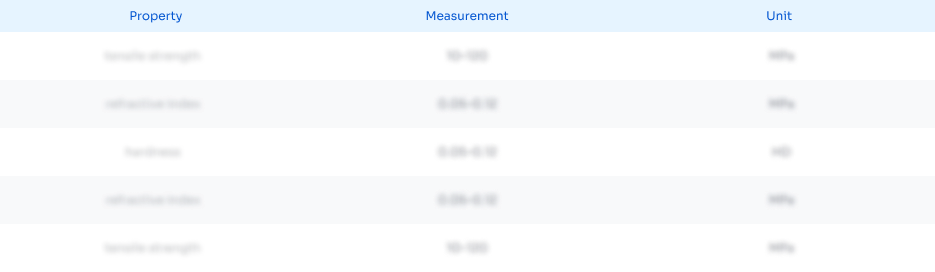
Abstract
Description
Claims
Application Information

- R&D
- Intellectual Property
- Life Sciences
- Materials
- Tech Scout
- Unparalleled Data Quality
- Higher Quality Content
- 60% Fewer Hallucinations
Browse by: Latest US Patents, China's latest patents, Technical Efficacy Thesaurus, Application Domain, Technology Topic, Popular Technical Reports.
© 2025 PatSnap. All rights reserved.Legal|Privacy policy|Modern Slavery Act Transparency Statement|Sitemap|About US| Contact US: help@patsnap.com