Method for growing high-resistance thick layer silicon epitaxy on 6-inch heavily As-doped silicon substrate
A technology of silicon epitaxy and substrate, applied in the direction of electrical components, semiconductor/solid-state device manufacturing, circuits, etc., can solve the problems of long process time, high resistivity uniform epitaxial layer difficulty, etc., and achieve good uniformity and narrow transition zone Effect
- Summary
- Abstract
- Description
- Claims
- Application Information
AI Technical Summary
Problems solved by technology
Method used
Image
Examples
Embodiment 1
[0029] (1) Use hydrogen chloride gas with a purity ≥ 99.99% to corrode the base of the epitaxial furnace at high temperature to completely remove the residual deposits on the base. The temperature is set at 1090°C, and the flow rate of hydrogen chloride gas is set at 5 L / min. The etching time was set to 10 min;
[0030] (2) Load the silicon substrate into the pit of the base of the epitaxial furnace, and use nitrogen and hydrogen with a purity of ≥99.999% to purge the cavity of the epitaxial furnace for 8 minutes in sequence, and set the gas flow rate to 100 L / min;
[0031] (3) Use hydrogen chloride gas to perform in-situ etching on the surface of the silicon substrate, which can polish the surface of the substrate and help to improve the lattice structure. Hydrogen gas is used to transport hydrogen chloride into the reaction chamber, and the hydrogen flow rate is set to 150 L / min, the hydrogen chloride flow rate is set to 2 L / min, the temperature is set to 1065°C, and the ti...
Embodiment 2
[0038](1) Use hydrogen chloride gas with a purity ≥ 99.99% to corrode the base of the epitaxial furnace at high temperature to completely remove the residual deposits on the base. The temperature is set at 1080°C, and the flow rate of hydrogen chloride gas is set at 5 L / min. The etching time was set to 10 min.
[0039] (2) Load the silicon substrate into the pit of the base of the epitaxial furnace, and use nitrogen and hydrogen with a purity of ≥99.999% to purge the cavity of the epitaxial furnace for 8 minutes in sequence, and set the gas flow rate to 150 L / min.
[0040] (3) Use hydrogen chloride gas to perform in-situ etching on the surface of the silicon substrate, which can polish the surface of the substrate and help to improve the lattice structure. Hydrogen gas is used to transport hydrogen chloride into the reaction chamber, and the hydrogen flow rate is set to 150 L / min, the hydrogen chloride flow rate is set to 2 L / min, the temperature is set to 1070°C, and the tim...
Embodiment 3
[0047] (1) Use hydrogen chloride gas with a purity ≥ 99.99% to corrode the base of the epitaxial furnace at high temperature to completely remove the residual deposits on the base. The temperature is set at 1080°C, and the flow rate of hydrogen chloride gas is set at 5 L / min. The etching time was set to 10 min.
[0048] (2) Load the silicon substrate into the pit of the base of the epitaxial furnace, and use nitrogen and hydrogen with a purity ≥99.999% to purge the cavity of the epitaxial furnace for 10 minutes in sequence, and set the gas flow rate to 150 L / min.
[0049] (3) Use hydrogen chloride gas to perform in-situ etching on the surface of the silicon substrate, which can polish the surface of the substrate and help to improve the lattice structure. Hydrogen gas is used to transport hydrogen chloride gas into the reaction chamber, and the hydrogen flow rate is set to 150 L / min, the hydrogen chloride flow rate is set to 1 L / min, the temperature is set to 1070°C, and the ...
PUM
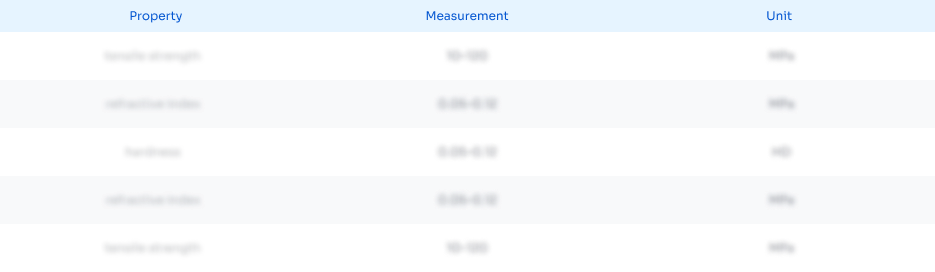
Abstract
Description
Claims
Application Information

- Generate Ideas
- Intellectual Property
- Life Sciences
- Materials
- Tech Scout
- Unparalleled Data Quality
- Higher Quality Content
- 60% Fewer Hallucinations
Browse by: Latest US Patents, China's latest patents, Technical Efficacy Thesaurus, Application Domain, Technology Topic, Popular Technical Reports.
© 2025 PatSnap. All rights reserved.Legal|Privacy policy|Modern Slavery Act Transparency Statement|Sitemap|About US| Contact US: help@patsnap.com