An electric furnace flue gas waste heat full vaporization, regenerative recovery system and its working method
A flue gas waste heat and recovery system technology, which is applied in the steam generation method using heat carrier, furnace, waste heat treatment, etc., can solve problems such as open welding of welding points, complex system layout, and impact on system operation safety, and increase waste heat absorption , increase steam volume, save system investment and floor space
- Summary
- Abstract
- Description
- Claims
- Application Information
AI Technical Summary
Problems solved by technology
Method used
Image
Examples
Embodiment 1
[0049] An electric furnace flue gas waste heat full vaporization, regenerative recovery system, comprising an electric furnace body 1, a flue gas channel 2, a flue gas channel 2 3, a dust collector 4, and a chimney 5; the top flue gas of the electric furnace body 1 The flue gas channel one 2 is connected to the dust collector 4; the internal flue gas of the electric furnace body 1 is connected to the dust collector 4 through the fourth hole 16 of the electric furnace body and the flue gas channel two 3; the flue gas Passage 2 3 includes flow guiding device 12, combustion settling chamber 13, convection heat exchange evaporator 18 and economizer 19 connected in sequence, and intermittent High-temperature flue gas heat storage device 14 and convective heat exchange superheater 17 .
Embodiment 2
[0051] An electric furnace flue gas waste heat full vaporization and regenerative recovery system as described in Example 1, the difference is that in the electric furnace body 1, the flow guide device 12, the combustion settling chamber 13, and the convective heat exchange superheater 17 , The convection heat exchange evaporator 18 and the economizer 19 are respectively equipped with cooling pipes for the furnace body of the electric furnace, cooling pipes for the diversion device, cooling pipes for the combustion and settling chamber, cooling pipes for the convective heat exchange superheater, and convection heat exchangers. The heat evaporator cooling pipe and the economizer cooling pipe; the flue gas channel 2 3 also includes a steam drum 15, and the steam drum 15 is respectively connected with the electric furnace body cooling pipe and the flow guiding device cooling pipe through the circulation pipeline. The pipe is connected with the cooling pipe of the combustion settli...
Embodiment 3
[0053] An electric furnace flue gas waste heat full vaporization and regenerative recovery system as described in Example 2, the difference is that the steam drum 15 is connected with the electric furnace body cooling pipes, the diversion device cooling pipes and the combustion settling chamber cooling pipes A forced circulation pump 20 is arranged on the connected circulation pipeline.
[0054] The flue gas channel 2 3 also includes a boiler feed water pump 21, a deaerator 22 and a boiler feed water device 23, and the inlet end of the economizer cooling pipe is sequentially connected with the boiler feed water pump 21, the deaerator 22 and the boiler feed water device 23, and the outlet end of the economizer cooling pipe is connected with the steam drum 15.
PUM
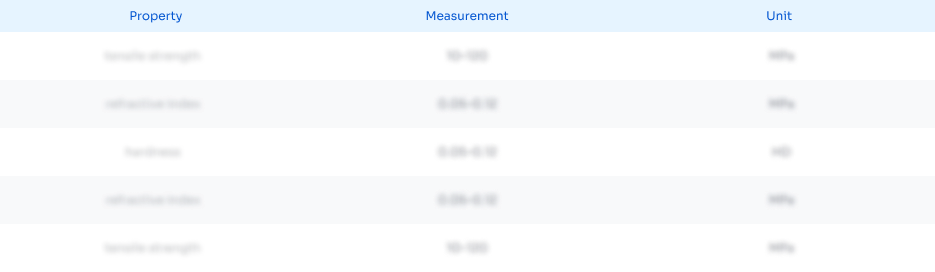
Abstract
Description
Claims
Application Information

- R&D
- Intellectual Property
- Life Sciences
- Materials
- Tech Scout
- Unparalleled Data Quality
- Higher Quality Content
- 60% Fewer Hallucinations
Browse by: Latest US Patents, China's latest patents, Technical Efficacy Thesaurus, Application Domain, Technology Topic, Popular Technical Reports.
© 2025 PatSnap. All rights reserved.Legal|Privacy policy|Modern Slavery Act Transparency Statement|Sitemap|About US| Contact US: help@patsnap.com