Preparation method of alkaline battery negative gel and alkaline battery negative gel
A technology of alkaline batteries and gelling agents, applied in the field of polymers, can solve the problems affecting the impact resistance of alkaline batteries, storage and transportation performance, processing and filling performance, reducing the crosslinking uniformity of products, and difficult control of polymerization reactions, etc., to achieve Effect of good performance, short gelation time, excellent impact resistance
- Summary
- Abstract
- Description
- Claims
- Application Information
AI Technical Summary
Problems solved by technology
Method used
Image
Examples
Embodiment 1
[0032] In a 1000mL five-necked flask equipped with a glass air guide tube, a reflux condensing device, a stirrer, and a thermometer, add 100g of acrylic acid, 590g of benzene, and 0.4g of polyoxyethylene (30) dipolyhydroxystearate. Under stirring, the temperature was raised to 70°C.
[0033] Dissolve 0.6g of bis(3,5,5-trimethylhexanoyl) peroxide in 60g of benzene, then dissolve 0.94g of pentaerythritol triallyl ether in 40g of benzene; -trimethylhexanoyl) and pentaerythritol triallyl ether started to drop at the same time, wherein bis(3,5,5-trimethylhexanoyl) peroxide was added dropwise for 4h, pentaerythritol triallyl ether was added dropwise for 3h, The reaction temperature was 70°C. After all the dropwise addition was completed, the reaction was terminated after the temperature was kept at 70° C. for 2 h.
[0034] After the reaction, the reaction slurry was suction-filtered, and then dried in a vacuum oven for 12 hours at a drying temperature of 90° C. and a pressure of -...
Embodiment 2-7
[0036] In a 1000mL five-necked flask equipped with a glass air guide tube, a reflux condensing device, a stirrer, and a thermometer, add 100g of acrylic acid, 590g of benzene, and 0.4g of polyoxyethylene (30) dipolyhydroxystearate. Heat up to the reaction temperature as recorded in Table 1 under stirring.
[0037] The initiator as recorded in Table 1 was dissolved in 60g of benzene, and the crosslinking agent as recorded in Table 1 was dissolved in 40g of benzene. The initiator of embodiment 2-7 and cross-linking agent start dropwise simultaneously, and dropwise time and reaction temperature are as recorded in table 1.
[0038] After all the dropwise addition was completed, the reaction was terminated after 2 h at the heat preservation temperature recorded in Table 1. After the reaction, the reaction slurry was suction-filtered, and then dried in a vacuum oven for 12 hours at a drying temperature of 90° C. and a pressure of -0.095 MPa. After drying, a white powder gel was obt...
Embodiment 8
[0043] In a 1000mL five-neck flask equipped with a glass air guide tube, reflux condensing device, stirrer, and thermometer, add 100g of acrylic acid, 590g of benzene, 0.5g of methacrylic acid, and 0.4g of polyoxyethylene (30) dipolyhydroxystearate , stirred and heated to 70°C under the condition of blowing nitrogen.
[0044] Dissolve 0.6 g of bis(3,5,5-trimethylhexanoyl) oxide in 60 g of benzene, and dissolve 0.94 g of pentaerythritol triallyl ether in 40 g of benzene. Mix the above two solutions evenly and drop them together for a total of 3 hours. The reaction temperature is 70°C. After the dropwise addition, keep warm at 70°C for 2 hours to end the reaction.
[0045] After the reaction, the reaction slurry was suction-filtered, and then dried in a vacuum oven for 12 hours at a drying temperature of 90° C. and a pressure of -0.095 MPa. After drying, a white powder gel was obtained.
PUM
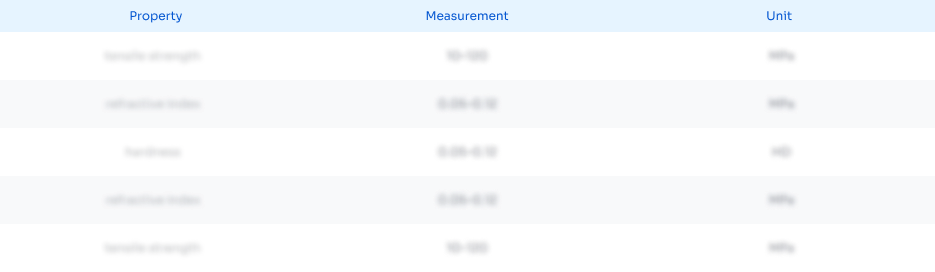
Abstract
Description
Claims
Application Information

- Generate Ideas
- Intellectual Property
- Life Sciences
- Materials
- Tech Scout
- Unparalleled Data Quality
- Higher Quality Content
- 60% Fewer Hallucinations
Browse by: Latest US Patents, China's latest patents, Technical Efficacy Thesaurus, Application Domain, Technology Topic, Popular Technical Reports.
© 2025 PatSnap. All rights reserved.Legal|Privacy policy|Modern Slavery Act Transparency Statement|Sitemap|About US| Contact US: help@patsnap.com