Method used for synthesizing 1,5,7-Triazabicyclo[4.4.0]dec-5-ene (TBD) via phase-transfer catalysis
A technology of phase transfer catalysis and phase transfer catalyst, applied in organic chemistry and other directions, can solve the problems of slow reaction rate, high reaction temperature, difficult product TBD purification, etc., and achieve the effect of short time and low reaction temperature.
- Summary
- Abstract
- Description
- Claims
- Application Information
AI Technical Summary
Problems solved by technology
Method used
Examples
Embodiment 1
[0023] Add the aqueous solution 20mL (5mmol / mL) of GHC in the 100mL reactor that is equipped with reflux condenser and electric stirring equipment, the mesitylene solution 20mL (5.0mmol / mL) of APA, the macroporous anion exchange resin ( D201) 0.29g, reacted for 10h under the protection of argon at 80°C.
[0024] After the reaction is completed, the reaction mixture is firstly recovered by filtration for D201 resin (recovered resin is washed and dried for repeated synthesis experiments), and then the water-oil two-phase system from which the resin has been filtered is recovered by a separatory funnel for oil phase mesitylene. After the aqueous phase was rotary evaporated, a light yellow viscous liquid was obtained. The latter was extracted with 30 mL of dichloromethane. After the extract was rotary evaporated to recover the dichloromethane, the colorless oily liquid was placed in the freezer of the refrigerator at -14°C for 8 hours, and then placed at room temperature (15-25°C)...
Embodiment 2
[0026] Add 20mL (5.5mmol / mL) of GHC's aqueous solution, 20mL (5.0mmol / mL) of APA's mesitylene solution to the 100mL reaction kettle equipped with reflux condenser and electric stirring equipment, pretreated macroporous anion exchange resin (D201) 0.42g, react under argon protection at 105°C for 8h.
[0027] After the reaction is completed, the reaction mixture is firstly recovered by filtration for D201 resin (recovered resin is washed and dried for repeated synthesis experiments), and then the water-oil two-phase system from which the resin has been filtered is recovered by a separatory funnel for oil phase mesitylene. After the aqueous phase was rotary evaporated, a light yellow viscous liquid was obtained. The latter was extracted with 30 mL of dichloromethane. After the extract was rotary evaporated to recover the dichloromethane, the colorless oily liquid was placed in the freezer of the refrigerator at -14°C for 10 hours, and then placed at room temperature (15-25°C) unt...
Embodiment 3
[0029] Add 20mL (6.0mmol / mL) of GHC's aqueous solution, 20mL (5.0mmol / mL) of APA's mesitylene solution, and pretreated macroporous anion exchange resin into a 100mL reaction kettle equipped with a reflux condenser and electric stirring equipment. (D201) 0.57g, reacted under argon protection at 120°C for 9h.
[0030] After the reaction is completed, the reaction mixture is firstly recovered by filtration to recover the D201 resin (the recovered resin is washed and dried for repeated synthesis experiments), and then the oil phase mesitylene is recovered from the water-oil two-phase system from which the resin has been filtered out by a separatory funnel. After the aqueous phase was rotary evaporated, a light yellow viscous liquid was obtained. The latter was extracted with 30 mL of dichloromethane. After the extract was rotary evaporated to recover the dichloromethane, the colorless oily liquid was placed in the freezer of the refrigerator at -14°C for 12 hours, and then placed ...
PUM
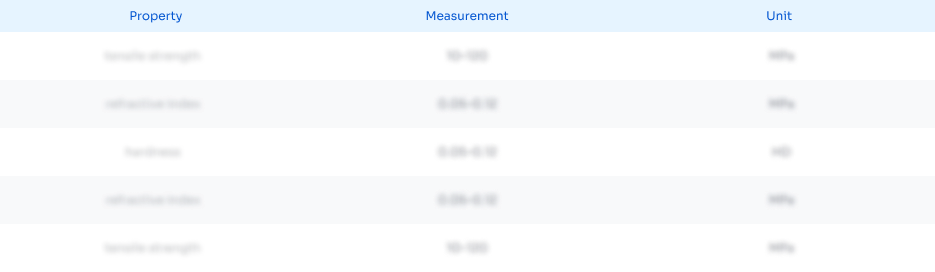
Abstract
Description
Claims
Application Information

- Generate Ideas
- Intellectual Property
- Life Sciences
- Materials
- Tech Scout
- Unparalleled Data Quality
- Higher Quality Content
- 60% Fewer Hallucinations
Browse by: Latest US Patents, China's latest patents, Technical Efficacy Thesaurus, Application Domain, Technology Topic, Popular Technical Reports.
© 2025 PatSnap. All rights reserved.Legal|Privacy policy|Modern Slavery Act Transparency Statement|Sitemap|About US| Contact US: help@patsnap.com