Method for preparing cyclohexene oxide by using micro flow field reaction technique
A technology of epoxy cyclohexane and microfluidic field, applied in organic chemistry and other directions, can solve the problems of difficult reaction control, high cost, low efficiency, etc., and achieve the effects of high yield and conversion rate, and easy and low-cost raw materials
- Summary
- Abstract
- Description
- Claims
- Application Information
AI Technical Summary
Problems solved by technology
Method used
Image
Examples
Embodiment 1
[0035]Inject the mixed solution of m-chlorobenzoyl chloride, hydrogen peroxide and sodium hydroxide into the first microstructure reactor of the microchannel modular reaction device, the molar ratio of m-chlorobenzoyl chloride and hydrogen peroxide is 1:4, hydrogen peroxide and hydrogen The molar ratio of sodium oxide is 1:1, and stay at 10°C for 0.5min; the output from the first microstructure reactor is mixed with the acidic dichloromethane solution and injected into the oil-water separation device, and the dichloromethane solution in the lower layer is mixed with cyclohexene After mixing, pass through the micro-mixer and the second micro-structure reactor successively, wherein the molar ratio of cyclohexene and m-chloroperoxybenzoic acid is controlled to be 1:1, stay at 20°C for 10 minutes, and the second micro-structure reactor exits The raw material was introduced into a separator, and the organic phase was washed with 5wt% sodium carbonate solution and distilled water to ...
Embodiment 2
[0037] Inject the mixed solution of m-chlorobenzoyl chloride, hydrogen peroxide and sodium hydroxide into the first microstructure reactor of the microchannel modular reaction device, the mol ratio of m-chlorobenzoyl chloride and hydrogen peroxide is 1:8, hydrogen peroxide and hydrogen The molar ratio of sodium oxide is 1:4, and stay at 40°C for 3 minutes; the output from the first microstructure reactor is mixed with acidic dichloromethane solution and injected into the oil-water separation device, and the dichloromethane solution in the lower layer is mixed with cyclohexene After passing through the micro-mixer and the second micro-structure reactor successively, the molar ratio of cyclohexene and m-chloroperoxybenzoic acid is controlled to be 1:6, and it stays at 40° C. for 20 minutes, and the second micro-structure reactor discharges Imported into a separator, the organic phase was washed with 5wt% sodium carbonate solution and distilled water to pH = 7.0, and dried to obta...
Embodiment 3
[0039] Inject the mixed solution of m-chlorobenzoyl chloride, hydrogen peroxide and sodium hydroxide into the first microstructure reactor of the microchannel modular reaction device, the mol ratio of m-chlorobenzoyl chloride and hydrogen peroxide is 1:6, hydrogen peroxide and hydrogen The molar ratio of sodium oxide is 1:2, and stay at 30°C for 2 minutes; the output of the first microstructure reactor is mixed with the acidic dichloromethane solution and injected into the oil-water separation device, and the dichloromethane solution in the lower layer is mixed with cyclohexene After passing through the micro-mixer and the second micro-structure reactor successively, the molar ratio of cyclohexene and m-chloroperoxybenzoic acid is controlled to be 1:4, and it stays at 30° C. for 15 minutes, and the second micro-structure reactor discharges Introduce it into a separator, wash the organic phase with 5wt% sodium carbonate solution and distilled water to pH = 7.0, and dry to obtain...
PUM
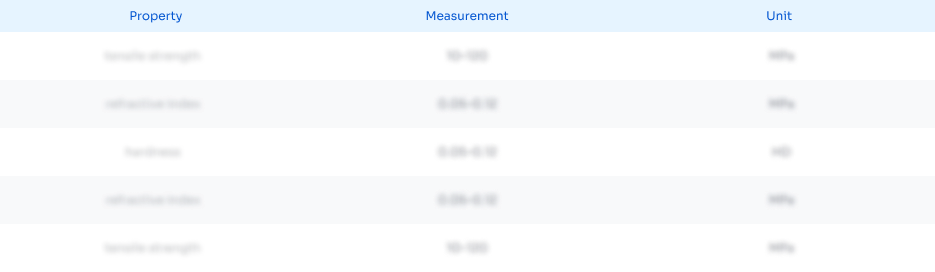
Abstract
Description
Claims
Application Information

- R&D
- Intellectual Property
- Life Sciences
- Materials
- Tech Scout
- Unparalleled Data Quality
- Higher Quality Content
- 60% Fewer Hallucinations
Browse by: Latest US Patents, China's latest patents, Technical Efficacy Thesaurus, Application Domain, Technology Topic, Popular Technical Reports.
© 2025 PatSnap. All rights reserved.Legal|Privacy policy|Modern Slavery Act Transparency Statement|Sitemap|About US| Contact US: help@patsnap.com