Method and device for reducing metal dust in electric wire and cable drawing process
A wire drawing process, wire and cable technology, applied in the field of metal dust reduction, can solve problems such as energy waste, environmental hazards, and unsmooth cooling circulation, and achieve the effects of improving safety performance, preventing oxidation, and fast circulation
- Summary
- Abstract
- Description
- Claims
- Application Information
AI Technical Summary
Problems solved by technology
Method used
Image
Examples
Embodiment 1
[0015] This embodiment provides a method of decreased metal powder dandruff in the process of drawing wires and cables. Installing a heating pipe before the brushed device enters the line, seal the two ends of the heating pipe with a high temperature -resistant material.Leave the import and export corresponding to the diameter size of the metal rod material that needs to be pulled. The metal rod material that needs to be drawn will be heated through the heating pipe before entering the first mold of the drawing device.The temperature in the heating pipe is set to 300-350 ° C; for the metal rod material of aluminum and aluminum alloy, the temperature in the heating pipe is set to 300-320 ° C.
[0016] In order to soften the metal before entering the mold and not be oxidized at this temperature, a heating pipe is installed between the rod material and the drawing device, and the metal rod material is seal.The heating pipe is made of temperature -resistant and stainless steel, which ...
Embodiment 2
[0019] This embodiment is a device for decreased metal powder dandruff in the process of wire and cables used for embodiments 1. The structure is figure 1 It shows that the heating pipe 1 with heating devices is set inside. The heating pipe 1 is set in front of the wires of the wire and cable drawing device.There is an import and export corresponding to the diameter size of the metal rod that needs to be pulled. The metal rod material that needs to be drawn is required to first enter the first mold of the drawing device through the heating pipe.The heating device is the heating resistance wire 3 set on the inner wall of the heating pipe, and the outer wall of the heating pipe is wrapped in 4 insulation cotton.High -temperature -resistant material sealing cushion is a high -temperature resistance ceramic silicone sealing cushion.
[0020] The above embodiments start with the dual start of the process details and the equipment improvement, and use the line metal rod soft -to -reduce...
PUM
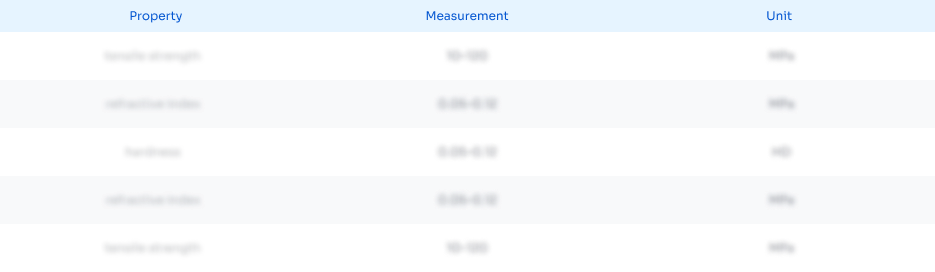
Abstract
Description
Claims
Application Information

- R&D
- Intellectual Property
- Life Sciences
- Materials
- Tech Scout
- Unparalleled Data Quality
- Higher Quality Content
- 60% Fewer Hallucinations
Browse by: Latest US Patents, China's latest patents, Technical Efficacy Thesaurus, Application Domain, Technology Topic, Popular Technical Reports.
© 2025 PatSnap. All rights reserved.Legal|Privacy policy|Modern Slavery Act Transparency Statement|Sitemap|About US| Contact US: help@patsnap.com