Process for preparing tilmicosin enteric-coated pellet by centrifuge method
A technology of tilmicosin and centrifugal pellet making, which is applied in the technical field of preparation of tilmicosin enteric-coated pellets by centrifugal method, which can solve the problems of poor palatability of tilmicosin, uneven coating thickness, and exclusion of raw materials In vitro and other problems, to achieve the effect of convenient centrifugal pellet making process, solving adverse reactions and low cost
- Summary
- Abstract
- Description
- Claims
- Application Information
AI Technical Summary
Problems solved by technology
Method used
Image
Examples
Embodiment 1
[0049] Each raw material is weighed according to the finished product containing the following mass percentages:
[0050] Tilmicosin: 23.3%;
[0051] Adhesive: 20% (formulated into 40% sucrose solution);
[0052] Microcrystalline cellulose: 17.2%;
[0053] Corn starch: 24.5%;
[0054] Coating solution: use 30% polyacrylic acid resin latex solution to prepare the coating solution according to the weight gain of the finished granules by 15%.
[0055] Grind the microcrystalline cellulose and cornstarch through an 80-mesh sieve and add tilmicosin to obtain a uniform powder. Then take 5Kg of the powder and gradually add it to the centrifugal pellet machine. At the same time, turn on the turntable and gradually spray it into the bonding agent. agent solution, the initial host speed is 100r / min, the spray speed is 200ml / min, the powder supply speed is 400g / min, and the damper is opened at 100m 3 / min; the time lasts for 6-8min to form a 60-80 mesh granule masterbatch. Then conti...
Embodiment 2
[0057] Each raw material is weighed according to the finished product containing the following mass percentages:
[0058] Tilmicosin: 25.8%;
[0059] Adhesive: 15% (formulated into 40% sucrose solution);
[0060] Microcrystalline cellulose: 24.2%;
[0061] Corn starch: 20%;
[0062] Coating solution: use 40% polyacrylic acid resin latex solution to prepare the coating solution according to the weight gain of the finished granules by 15%.
[0063] Grind the microcrystalline cellulose and cornstarch through an 80-mesh sieve and add tilmicosin to obtain a uniform powder. Then take 5Kg of the powder and add it to the centrifugal pellet machine. At the same time, turn on the turntable and gradually spray the adhesive solution, the initial host speed is 100r / min, the spray speed is 200ml / min, the powder supply speed is 400g / min, and the damper is opened at 100-120m 3 / min; the time lasts for 6-8min to form a 60-80 mesh granule masterbatch. Then continuously add the previously m...
Embodiment 3
[0065] According to the method described in Example 1, the obtained micropill finished product is carried out to morphology investigation, the mensuration of drug loading, the mensuration of encapsulation efficiency and the stripping release experiment under different environments; The dissolved pellets are 30-60 mesh spherical pellets with high true sphericity and uniform particle size (see figure 1 ), the drug loading is 20-25%, which is equivalent to the dosage, and the encapsulation efficiency is 100%. The pellets produced by the extrusion granulation method have irregular spherical shape and non-uniform particle size (see image 3 ), the drug loading is 20-25%, which is equivalent to the dosage, and the encapsulation thickness is not uniform. The pellets formed by the drying method in the liquid are ellipsoidal, and the particle size is uneven, (see figure 2 ), the drug loading is 20-25%, which is equivalent to the dosage, and the pellets prepared by the in-liquid dryi...
PUM
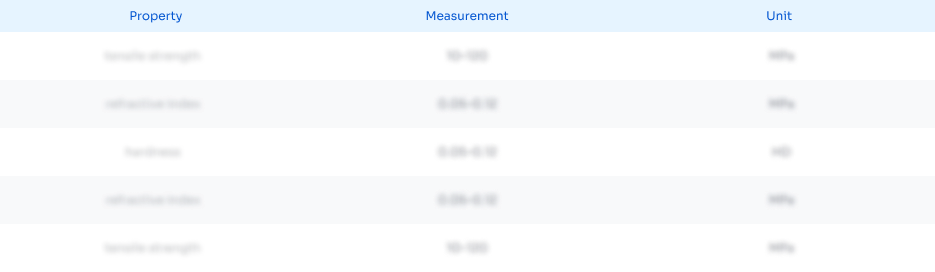
Abstract
Description
Claims
Application Information

- R&D
- Intellectual Property
- Life Sciences
- Materials
- Tech Scout
- Unparalleled Data Quality
- Higher Quality Content
- 60% Fewer Hallucinations
Browse by: Latest US Patents, China's latest patents, Technical Efficacy Thesaurus, Application Domain, Technology Topic, Popular Technical Reports.
© 2025 PatSnap. All rights reserved.Legal|Privacy policy|Modern Slavery Act Transparency Statement|Sitemap|About US| Contact US: help@patsnap.com