Thermal treatment technology for clutch disc hub
A technology for clutch discs and hubs, which is applied in the heat treatment process of clutch discs and hubs, and can solve problems such as failure to meet the fatigue life requirements of clutch discs and hubs
- Summary
- Abstract
- Description
- Claims
- Application Information
AI Technical Summary
Problems solved by technology
Method used
Image
Examples
Embodiment Construction
[0016] Such as figure 1 As shown, in the heat treatment process of the clutch disc hub in the embodiment of the present invention, it includes the following steps:
[0017] S1. Select 20CrMo alloy structural steel as the manufacturing material of the clutch disc hub, put the 20CrMo disc hub into the heating furnace for heating, and control the carbon potential CP of the furnace gas at 0.5 to 0.7. The initial temperature in the furnace is about 850-900°C, put the 20CrMo hub into the high-temperature furnace, the 20CrMo hub will absorb part of the heat, and then the temperature in the furnace will start to rise, so figure 1 At the beginning, it was a V-shaped fold line. In 20CrMo alloy structural steel, the mass ratio of various elements is: C 0.17-0.24%; Si0.17-0.37%; Mn 0.40-0.70%; Mo 0.15-0.25%; Cr 0.80-1.10%; P≤0.03% ; S≤0.025%, the rest is Fe. Due to the increase of C content and the addition of Cr and Mo elements, the hardness of the center of the hub after carbonitridi...
PUM
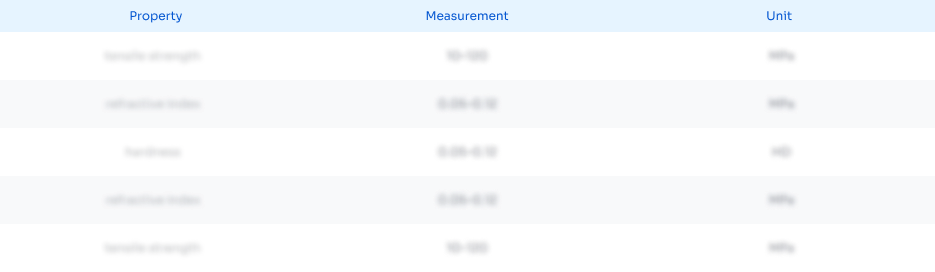
Abstract
Description
Claims
Application Information

- R&D
- Intellectual Property
- Life Sciences
- Materials
- Tech Scout
- Unparalleled Data Quality
- Higher Quality Content
- 60% Fewer Hallucinations
Browse by: Latest US Patents, China's latest patents, Technical Efficacy Thesaurus, Application Domain, Technology Topic, Popular Technical Reports.
© 2025 PatSnap. All rights reserved.Legal|Privacy policy|Modern Slavery Act Transparency Statement|Sitemap|About US| Contact US: help@patsnap.com