Preparation method of synthetic paper based on plant modified fibers
A technology of modified fiber and plant fiber, which is applied in the field of synthetic paper, can solve the problems of low strength and low strength of synthetic paper, and achieve the effect of improving tensile tension and strength, and improving compatibility
- Summary
- Abstract
- Description
- Claims
- Application Information
AI Technical Summary
Problems solved by technology
Method used
Examples
Embodiment 1
[0022] Step 1. Modification of plant fiber: pulverize 30Kg of corn fiber powder, then mix it with 10Kg of malic acid, and perform heating and pressure treatment. The absolute pressure in the process is 200kPa, the temperature is 150℃, and the treatment time is 5 hours. Dry again
[0023] Step 2. After mixing the dried product obtained in Step 1 with 3Kg of ethylene-vinyl alcohol copolymer and 5Kg of glycerin, heat activation treatment. The temperature of the heat activation treatment is 150℃ and the treatment time is 3 hours to obtain modified plants. Fiber powder
[0024] The third step is to combine polyethylene 30Kg, polypropylene 10Kg, ethylene-vinyl acetate copolymer polymer 1Kg, polycarbonate 3Kg, polystyrene particles 3Kg, plant fiber 40Kg, perlite 5Kg, surfactant 2Kg, talc 4Kg of powder, 3Kg of polyimide fiber, 2Kg of paraffin oil, 2Kg of pentaerythritol, 1Kg of antioxidant, mix well to obtain a mixture;
[0025] The fourth step is to feed the mixture into a twin-screw extr...
Embodiment 2
[0027] Step 1. Modification of plant fiber: crush 50Kg of corn fiber powder, then mix it with 15Kg of malic acid, and heat and press. The absolute pressure in the process is 400kPa, the temperature is 200℃, and the treatment time is 20 hours. Dry again
[0028] Step 2. After mixing the dried product obtained in Step 1 with 6Kg of ethylene-vinyl alcohol copolymer and 10Kg of glycerin, heat activation treatment. The temperature of the heat activation treatment is 190℃ and the treatment time is 6 hours to obtain modified plants. Fiber powder
[0029] Step 3: Combine polyethylene 40Kg, polypropylene 20Kg, ethylene-vinyl acetate copolymer polymer 3Kg, polycarbonate 7Kg, polystyrene particles 7Kg, plant fiber 60Kg, perlite 5Kg, surfactant 3Kg, talc 4Kg of powder, 3Kg of polyimide fiber, 2Kg of paraffin oil, 2Kg of pentaerythritol, 2Kg of antioxidant, and mix well to obtain a mixture;
[0030] The fourth step is to feed the mixture into a twin-screw extruder for extrusion and granulation,...
Embodiment 3
[0032] Step 1: Modification of plant fiber: pulverize 40Kg of corn fiber powder, then mix it with 12Kg of malic acid, and perform heating and pressure treatment. The absolute pressure in the process is 300kPa, the temperature is 180°C, and the treatment time is 12 hours. Dry again
[0033] Step 2. After mixing the dried product obtained in Step 1 with 5Kg of ethylene-vinyl alcohol copolymer and 8Kg of glycerin, heat activation treatment. The temperature of the heat activation treatment is 180°C and the treatment time is 5 hours to obtain modified plants. Fiber powder
[0034] The third step is to combine polyethylene 35Kg, polypropylene 15Kg, ethylene-vinyl acetate copolymer polymer 2Kg, polycarbonate 5Kg, polystyrene particles 5Kg, plant fiber 50Kg, perlite 5Kg, surfactant 2Kg, talc 4Kg of powder, 3Kg of polyimide fiber, 2Kg of paraffin oil, 2Kg of pentaerythritol, 1Kg of antioxidant, mix well to obtain a mixture;
[0035] The fourth step is to feed the mixture into a twin-screw e...
PUM
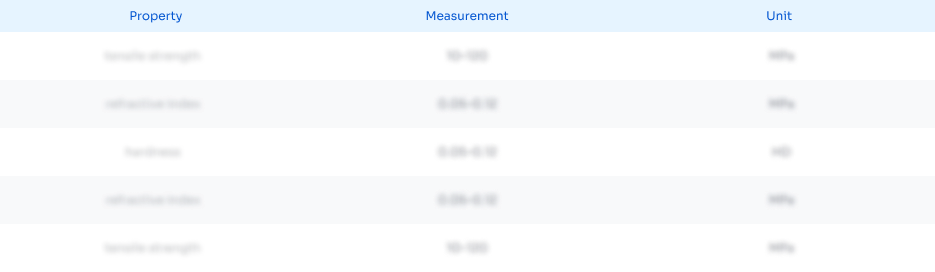
Abstract
Description
Claims
Application Information

- Generate Ideas
- Intellectual Property
- Life Sciences
- Materials
- Tech Scout
- Unparalleled Data Quality
- Higher Quality Content
- 60% Fewer Hallucinations
Browse by: Latest US Patents, China's latest patents, Technical Efficacy Thesaurus, Application Domain, Technology Topic, Popular Technical Reports.
© 2025 PatSnap. All rights reserved.Legal|Privacy policy|Modern Slavery Act Transparency Statement|Sitemap|About US| Contact US: help@patsnap.com