Platinum recovery refining process
A process and process step technology, applied in the field of platinum recovery and refining process, can solve the problems of low production efficiency, long production cycle, large solution processing capacity, etc., and achieve improved yield and quality, reduced production cost, and good operability. Effect
- Summary
- Abstract
- Description
- Claims
- Application Information
AI Technical Summary
Problems solved by technology
Method used
Examples
Embodiment 1
[0020] A platinum recovery and refining process, comprising the following process steps:
[0021] a. Carbonize 100kg of platinum-containing material at 750°C for 1.5 hours;
[0022] b. After cooling to room temperature, add 200kg of aqua regia to dissolve, and control the temperature between 65°C until the dissolution is complete;
[0023] c. Add 300kg ammonium chloride to precipitate for 0.5 hour. After the precipitation is completed, ammonium chloroplatinate is filtered and washed;
[0024] d. Add 200kg of sodium hydroxide to dissolve, and complete the dissolution after 20 minutes to form a solution;
[0025] e. After heating the solution in step d to 45° C., 200 kg of hydrazine hydrate was added for reduction. The reaction time was 0.5 hours, and the recovery of platinum was completed;
Embodiment 2
[0028] A platinum recovery and refining process, comprising the following process steps:
[0029] a. Carbonize 100kg of platinum-containing material at 800°C for 2 hours;
[0030] b. After cooling to room temperature, add 250kg of aqua regia to dissolve, and control the temperature between 70°C until the dissolution is complete;
[0031] c. Add 400kg ammonium chloride to precipitate for 1 hour. After the precipitation is completed, ammonium chloroplatinate is filtered and washed;
[0032] d. Add 250kg of sodium hydroxide to dissolve, and complete the dissolution after 30 minutes to form a solution;
[0033] e, heating the solution in step d to 50°C, adding 250kg of hydrazine hydrate for reduction, the reaction time is 1 hour, and the recovery of platinum is completed;
Embodiment 3
[0036] A platinum recovery and refining process, comprising the following process steps:
[0037] a. Carbonize 100kg of platinum-containing material at 850°C for 2.5 hours;
[0038] b. After cooling to room temperature, add 300kg of aqua regia to dissolve, and control the temperature between 75°C until the dissolution is complete;
[0039] c. Add 500kg ammonium chloride to precipitate for 1.5 hours. After the precipitation is completed, ammonium chloroplatinate is filtered and washed;
[0040] d. Add 300kg of sodium hydroxide to dissolve, and complete the dissolution after 40 minutes to form a solution;
[0041] e. After heating the solution in step d to 55° C., 300 kg of hydrazine hydrate was added for reduction. The reaction time was 1.5 hours, and the recovery of platinum was completed;
[0042] f. Drying the reduced platinum powder.
[0043] The beneficial effects of the invention are: the time required for the recovery process is greatly shortened, the production cost ...
PUM
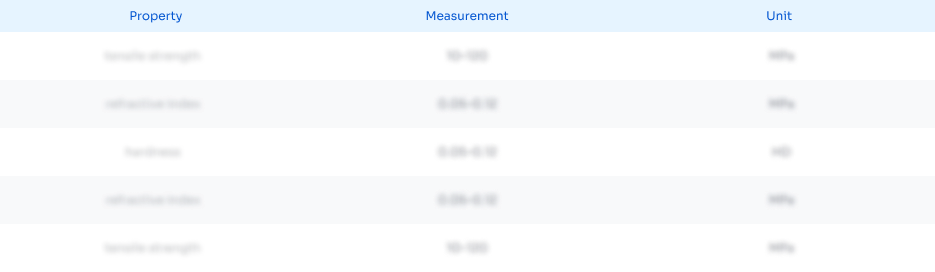
Abstract
Description
Claims
Application Information

- Generate Ideas
- Intellectual Property
- Life Sciences
- Materials
- Tech Scout
- Unparalleled Data Quality
- Higher Quality Content
- 60% Fewer Hallucinations
Browse by: Latest US Patents, China's latest patents, Technical Efficacy Thesaurus, Application Domain, Technology Topic, Popular Technical Reports.
© 2025 PatSnap. All rights reserved.Legal|Privacy policy|Modern Slavery Act Transparency Statement|Sitemap|About US| Contact US: help@patsnap.com