High-concentration anti-electrostatic master batch and preparation method thereof
An antistatic masterbatch, high-concentration technology, applied in the polymer field, can solve the problems that the antistatic agent is difficult to disperse evenly in the polymer material, the material cannot achieve the antistatic effect, and the antistatic agent is difficult to disperse evenly. Achieve low-cost, easy-to-operate, easy-to-mix results
- Summary
- Abstract
- Description
- Claims
- Application Information
AI Technical Summary
Problems solved by technology
Method used
Examples
Embodiment 1
[0039] A preparation method for high-concentration antistatic masterbatch, comprising the steps of:
[0040] (1) Fully mix 100g polyethylene, 800g polypropylene, 25g calcium carbonate, 50g butane, 5g glyceryl monostearate, and 1g oxidized polyethylene wax, melt and blend in an extruder, extrude, After cooling and granulating, the primary particles of the polymer are obtained; the primary particles of the polymer are then foamed to prepare a porous polymer carrier.
[0041] (2) Put the porous polymer carrier prepared in (1) at 50°C for 2 hours in an electric blast drying oven;
[0042] (3) Heat the liquid organic amine salt antistatic agent in a constant temperature water bath at 50°C for 3 hours;
[0043] (4) Add 100g of the porous polymer carrier dried in step (2) and 100g of the antistatic agent treated in step (3) into the stirring tank at the same time, until the antistatic agent is completely absorbed by the porous polymer carrier and then discharged , to produce 50% an...
Embodiment 2
[0045] (1) Fully mix 850g polystyrene, 10g barium sulfate, 10g carbon dioxide, 1g glyceryl monostearate, 1g oxidized polyethylene wax, 2g stearic acid amide, melt blend in an extruder, extrude After cooling and granulating, the primary particles of the polymer are obtained; then the primary particles of the polymer are foamed to prepare a porous polymer carrier.
[0046] (2) Put the porous polymer carrier prepared in (1) at 60°C for 1 hour in an electric blast drying oven;
[0047] (3) Heat the liquid organic amine salt antistatic agent in a constant temperature water bath at 90°C for 1 hour;
[0048] (4) Add 30g of the porous polymer carrier dried in step (2) and 170g of the antistatic agent treated in step (3) into the stirring tank at the same time, until the antistatic agent is completely absorbed by the porous polymer carrier and then discharged , Prepare 85% antistatic masterbatch.
Embodiment 3
[0050] (1) Fully mix 800g polystyrene, 150g polyethylene, 50g barium sulfate, 50g titanium dioxide, 20g carbon dioxide, 30g nitrogen, 5g glyceryl monostearate and 1g polysiloxane, and put them in the extruder Melt blending, extrusion, cooling and granulation to obtain the primary particles of the polymer; then foam the primary particles of the polymer to prepare a porous polymer carrier,
[0051] (2) Put the porous polymer carrier prepared in (1) at 55°C for 1.5h in an electric blast drying oven;
[0052](3) Heat the liquid organic amine salt antistatic agent in a constant temperature water bath at 70°C for 2 hours;
[0053] (4) Add 100g of the porous polymer carrier dried in step (2) and 300g of the antistatic agent treated in step (3) into the stirring tank at the same time, until the antistatic agent is completely absorbed by the porous polymer carrier and then discharged , to produce 75% antistatic masterbatch.
PUM
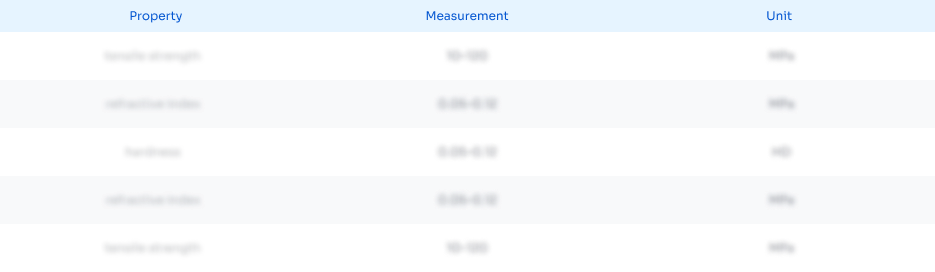
Abstract
Description
Claims
Application Information

- R&D
- Intellectual Property
- Life Sciences
- Materials
- Tech Scout
- Unparalleled Data Quality
- Higher Quality Content
- 60% Fewer Hallucinations
Browse by: Latest US Patents, China's latest patents, Technical Efficacy Thesaurus, Application Domain, Technology Topic, Popular Technical Reports.
© 2025 PatSnap. All rights reserved.Legal|Privacy policy|Modern Slavery Act Transparency Statement|Sitemap|About US| Contact US: help@patsnap.com