Blend modified rubber material
A rubber material, blending and modification technology, applied in the field of rubber material manufacturing, can solve the problems of poor wet grip performance of PU tires, high PU price, and adhesion problems, etc., to improve wet grip performance and wear resistance The effect of improving and improving the wear resistance
- Summary
- Abstract
- Description
- Claims
- Application Information
AI Technical Summary
Problems solved by technology
Method used
Examples
Embodiment 1
[0067] Embodiment 1 (comparative embodiment)
[0068] 1. Synthesis of PU prepolymer
[0069] Component A:
[0070] 80 / 20TDI: 65g
[0071] PPG (1000): 135g
[0072] Total: 200g
[0073] Synthesis method: PPG is heated to 70-130°C for vacuum dehydration, and after cooling, TDI is added to react at 60-90°C to prepare a prepolymer, and -NCO is controlled at about 10%.
[0074] Component B:
[0075] MOCA: 45g
[0076] PPG (1000): 65g
[0077] Total: 110g
[0078] Mixing method: Heat and melt MOCA, then add PPG and mix evenly.
[0079] 2. Natural rubber material A formula
[0080] NR: 1000g
[0082] N330: 360g
[0083] Accelerator DM: 12g
[0084] Sulfur: 25g
[0085] Antiaging agent IPPD: 10g
[0086] Total: 1457g
[0087] The natural rubber is plasticized and kneaded to obtain the natural rubber material A.
[0088] 3. Take the PU material and mix it evenly in the ratio of A:B=200:110, vulcanize and mold it at 100°C, and then grind it into...
Embodiment 2
[0096] 1. Synthesis of PU prepolymer
[0097] 80 / 20TDI: 100g
[0098] 1,4-butanediol: 8g
[0099] PPG (1000): 198.5g
[0100] Synthesis method: PPG is heated to 70-130°C for vacuum dehydration, after cooling, add 1,4-butanediol to mix, add TDI and react at 60-90°C to prepare a prepolymer, and the -NCO is controlled at about 7.89%.
[0101] 2. Natural rubber formula
[0102] Natural rubber compound formula is with embodiment 1.
[0103] The natural rubber is plasticized and mixed to obtain the rubber material A.
[0104]3. Take 300g of PU prepolymer, add 25g of TMP, mix evenly, weigh 97.5g and add it to 1000g of natural rubber compound A, mix evenly, calender, and extrude to obtain compound B, PU accounts for 8.9% of the total.
[0105] 4. Vulcanization condition: 150℃×30min, strip rubber for compression test.
[0106] 5. Akron abrasion machine test results:
[0107] Compound A: 0.66mg / m (measured in Example 1)
[0108] Compound B: 0.45mg / m
[0109] It can be seen from...
Embodiment 3
[0111] 1. Synthesis of PU prepolymer (same as Example 2).
[0112] 2. Natural rubber compound formula (same as embodiment 1).
[0113] The natural rubber is plasticized and mixed to obtain the rubber compound A.
[0114] 3. Take 77.5g of PU prepolymer and add it to 800g of natural rubber compound A and mix evenly to obtain compound B1; then take 18.5g of MOCA and add it to 200g of natural rubber compound A and mix evenly to obtain compound B2. Then mix B1 and B2 evenly, calender, and extrude to obtain the rubber material B. PU accounts for 8.8% of the total.
[0115] 4. Vulcanization condition: 150℃×30min, strip rubber for compression test.
[0116] 5. Akron abrasion machine test results:
[0117] Compound A: 0.66mg / m (measured in Example 1)
[0118] Compound B: 0.43mg / m
[0119] It can be seen from the test results that by adding a total amount of 8.8% of the PU material to the natural rubber material A, the wear resistance can be increased by about 34.8%.
PUM
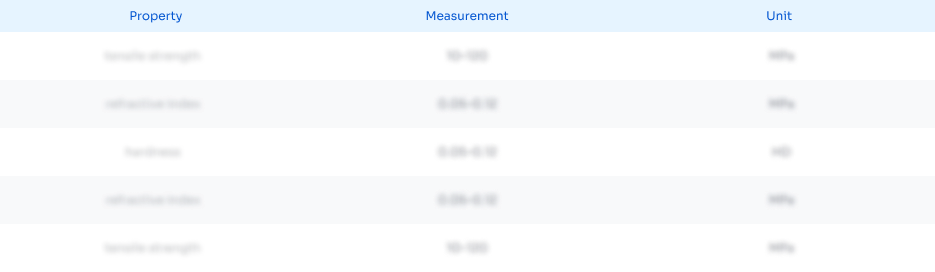
Abstract
Description
Claims
Application Information

- R&D Engineer
- R&D Manager
- IP Professional
- Industry Leading Data Capabilities
- Powerful AI technology
- Patent DNA Extraction
Browse by: Latest US Patents, China's latest patents, Technical Efficacy Thesaurus, Application Domain, Technology Topic, Popular Technical Reports.
© 2024 PatSnap. All rights reserved.Legal|Privacy policy|Modern Slavery Act Transparency Statement|Sitemap|About US| Contact US: help@patsnap.com