Electrochemical drawing process and electrochemical drawing device for metal wire material
A technology of drawing device and drawing process, which is applied in the field of metal drawing to achieve the effects of low equipment cost, high production safety and low current density
- Summary
- Abstract
- Description
- Claims
- Application Information
AI Technical Summary
Problems solved by technology
Method used
Image
Examples
Embodiment 1
[0032] An electrochemical drawing device for metal wire, such as figure 1 As mentioned above, a DC power supply 1 and an electrolytic cell 3 filled with electrolyte 2 are added on the basis of the traditional drawing device (composed of wire drawing machines 9 and 10 ); 5, the negative electrode of the DC power supply is communicated with the electrolyte 2 through the cathode stainless steel sheet 6; at the same time, insulating blocks 7 are respectively provided at both ends of the electrolytic cell 3, the wire drawing die 8 and the electrolytic cell 3 are insulated and separated, the wire material 5 and the electrolytic cell 3 Insulation and separation; the inner wall of the electrolytic cell 3 is coated with a layer of insulating epoxy resin to isolate the electrolyte 2 and the electrolytic cell 3 from each other.
Embodiment 2
[0034] This embodiment is an electrochemical drawing process of 4043 aluminum alloy, and the aluminum wire is drawn from Φ9.5 to Φ5 through 7 passes. In the example, the electrolyte formula is 20g / L NaOH, 25g / L Mobilbaosu 67 emulsified oil, and the remainder is distillation; the current density introduced in the drawing process is 40mA / cm 2 , the drawing speed is 0.10 m / s.
[0035] Compared with traditional drawing, the cumulative deformation of 4043 aluminum alloy in electrochemical drawing increases, and the drawing force decreases. 4043 aluminum alloy traditionally drawn to Φ5.8 needs to be annealed before drawing, while 4043 aluminum alloy can be drawn to Φ5 without annealing electrochemically. The drawing force during the drawing process decreased by 8%-18%, and the surface hardness of the wire after drawing decreased by 20%. Compared with electroplastic drawing, the introduced current density is extremely small.
Embodiment 3
[0037] This embodiment is an electrochemical drawing process of 2024 aluminum alloy, and the aluminum wire is drawn from Φ9.5 to Φ5 through 7 passes. In the example, the electrolyte formula is 40g / L NaOH, 30g / L Mobilbaosu 67 emulsified oil, and the remainder is distillation; the current density introduced in the drawing process is 50mA / cm 2 , the drawing speed is 0.17m / s.
[0038] Compared with traditional drawing, the electrochemical drawing of 2024 aluminum alloy reduces the number of annealing, the drawing force during the drawing process decreases by about 26%, and the surface hardness of the wire after drawing decreases by 21%. Compared with electroplastic drawing, the introduced current density is extremely small.
PUM
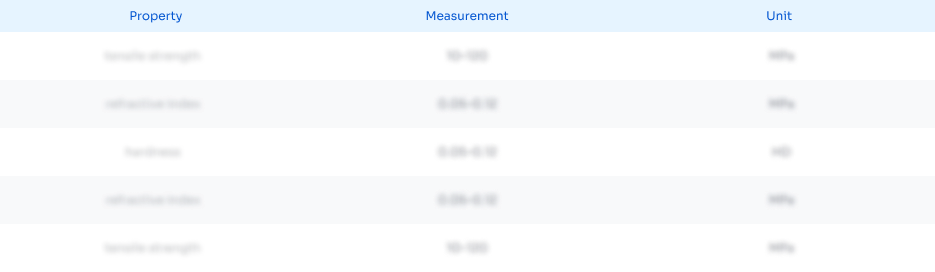
Abstract
Description
Claims
Application Information

- R&D Engineer
- R&D Manager
- IP Professional
- Industry Leading Data Capabilities
- Powerful AI technology
- Patent DNA Extraction
Browse by: Latest US Patents, China's latest patents, Technical Efficacy Thesaurus, Application Domain, Technology Topic, Popular Technical Reports.
© 2024 PatSnap. All rights reserved.Legal|Privacy policy|Modern Slavery Act Transparency Statement|Sitemap|About US| Contact US: help@patsnap.com