Catalyst for preparing alkane by catalytically hydrogenating biological oil
A bio-grease and catalytic hydrogenation technology, applied in physical/chemical process catalysts, metal/metal oxide/metal hydroxide catalysts, molecular sieve catalysts, etc., can solve problems such as polluted products, increased processing costs, and sulfur loss. Achieve the effects of reducing production costs, good catalytic effect, and alleviating the shortage of petrochemical energy
- Summary
- Abstract
- Description
- Claims
- Application Information
AI Technical Summary
Problems solved by technology
Method used
Image
Examples
Embodiment 1
[0018] The preparation of embodiment 1 Ni-Mo / Ce-ZSM-35 catalyst
[0019] Activate ZSM-35 in a muffle furnace at 400°C to 600°C for 2 hours, then add it to a certain concentration of cerium nitrate solution, stir at room temperature at a low speed for a certain period of time, and then wash the molecular sieve with a large amount of deionized water , centrifuge, and bake at 400° C. for 3 hours to 5 hours after being dried to obtain a cerium-modified ZSM-35 carrier. Under the condition of stirring at 20°C-60°C, dissolve the metal salts of nickel and molybdenum in deionized water, and stir thoroughly to obtain a solution, then add the solution to the prepared cerium-modified ZSM-35 catalyst carrier, and stir for 18h-25h , and then dry the obtained mixture in an air atmosphere of 100°C to 120°C, and then bake it in an air atmosphere of 600°C to 800°C for 4h to 6h to obtain a nickel content of 5% to 40% and a molybdenum content of 5%. ~40% catalyst.
Embodiment 2
[0020] Example 2 Ni-Mo / Ba-Al 2 o 3 Catalyst preparation
[0021] Calcining pseudo-boehmite at 600°C for 5h to 10h produces γ-Al 2 o 3 , impregnated with Ba(NO 3 ) 2 After the solution was dried overnight, it was calcined at 1000°C to 1200°C for 5 hours in an air atmosphere, and the content of BaO in the sample was determined by Ba(NO 3 ) 2 Concentration control to prepare BaO-modified γ-Al 2 o 3 Catalyst carrier. Under the condition of stirring at 20°C-60°C, dissolve the metal salts of nickel and molybdenum in deionized water, and stir thoroughly to obtain a solution, then add the solution to the prepared catalyst carrier, stir for 18h-25h, and then put the obtained mixture Drying in an air atmosphere at 100°C-120°C, and then calcining in an air atmosphere at 600°C-800°C for 4h-6h to obtain a catalyst with a nickel content of 10%-50% and a molybdenum content of 10%-30%.
Embodiment 3
[0022] Example 3 Ni-Mo / La-Al 2 o 3 Catalyst preparation
[0023] Al 2 o 3 powder, and then use a certain concentration of La(NO 3 ) 3 After solution impregnation, drying and calcination at 900 °C, lanthanum-modified Al 2 o 3 carrier. Add ammonia water to the salt solution containing nickel and molybdenum at 10°C to 30°C and stir to react, then lanthanum modifies Al 2 o 3 Add the carrier into the solution, adjust the pH value to 10, reflux at 100°C for 3h, filter and dry, and roast at 400°C for 5h to obtain the catalyst.
PUM
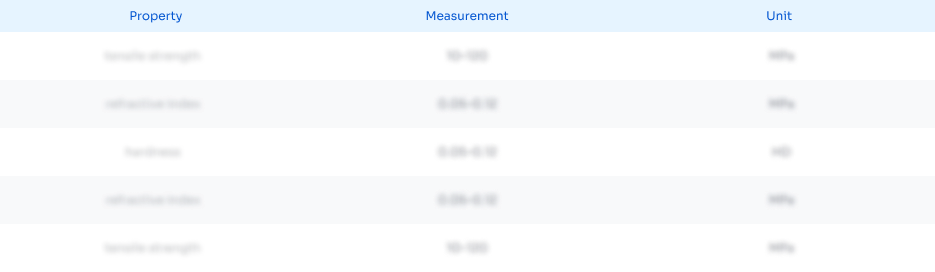
Abstract
Description
Claims
Application Information

- R&D
- Intellectual Property
- Life Sciences
- Materials
- Tech Scout
- Unparalleled Data Quality
- Higher Quality Content
- 60% Fewer Hallucinations
Browse by: Latest US Patents, China's latest patents, Technical Efficacy Thesaurus, Application Domain, Technology Topic, Popular Technical Reports.
© 2025 PatSnap. All rights reserved.Legal|Privacy policy|Modern Slavery Act Transparency Statement|Sitemap|About US| Contact US: help@patsnap.com