Turning, grinding, milling universal emulsion cutting oil, and production method thereof
A cutting oil and grinding technology, applied in grinding, milling general-purpose emulsified cutting oil, and turning fields, can solve the problems of poor anti-rust ability and easy rust on the workpiece surface
- Summary
- Abstract
- Description
- Claims
- Application Information
AI Technical Summary
Problems solved by technology
Method used
Examples
Embodiment 1
[0017] Raw materials and mass percentages used are as follows:
[0018] Sodium petroleum sulfonate 10~15%
[0019] Barium petroleum sulfonate 10~15%
[0020] Sodium ricinoleate 4~8%
[0021] Triethanolamine oleic acid soap 4~6%
[0022] NP-6 1~2%
[0023] 32# mechanical oil 18~22%
[0024] Defoamer 0.1~0.5%
[0025] Phosphating water quality regulator 4~6%
[0026] water balance.
[0027] A method for producing the above-mentioned general-purpose emulsified cutting oil for turning, grinding, and milling, which is characterized in that it is carried out as follows: add calculated and weighed water into the reaction kettle, heat it to 70~80°C, start the stirrer, and control the speed of 40 turn / min, then calculate and weigh sodium petroleum sulfonate, barium petroleum sulfonate, sodium ricinoleate, trietha...
Embodiment 2
[0030] Raw materials and mass percentages used are as follows:
[0031] Sodium Petroleum Sulfonate 15%
[0032] Barium Petroleum Sulfonate 10%
[0033] Sodium Ricinoleate 8%
[0034] Triethanolamine Oleic Soap 4%
[0035] NP-6 1%
[0036] 32# mechanical oil 22%
[0037] Defoamer 0.5%
[0038] Phosphating water conditioner 4%
[0039] water balance.
[0040] Production method is with embodiment 1.
[0041] During use, the embodiment of the present invention 1,2 is prepared the working liquid of 3% by mass percent, respectively as carbon steel, cast iron metal workpiece processing, cooling performance, lubricating performance, cleaning performance and antirust performance have obtained remarkable improvement, antirust period of more than two weeks.
PUM
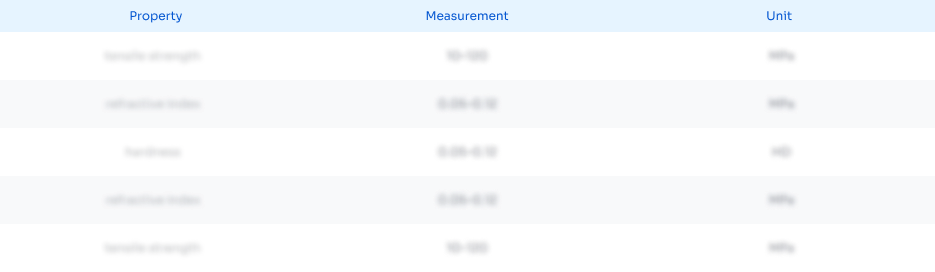
Abstract
Description
Claims
Application Information

- Generate Ideas
- Intellectual Property
- Life Sciences
- Materials
- Tech Scout
- Unparalleled Data Quality
- Higher Quality Content
- 60% Fewer Hallucinations
Browse by: Latest US Patents, China's latest patents, Technical Efficacy Thesaurus, Application Domain, Technology Topic, Popular Technical Reports.
© 2025 PatSnap. All rights reserved.Legal|Privacy policy|Modern Slavery Act Transparency Statement|Sitemap|About US| Contact US: help@patsnap.com