Alkaline chemical polishing method and adopted alkaline chemical polishing solution thereof
A chemical polishing and alkaline technology, applied in the field of metal surface treatment, can solve problems such as unfriendly environment, achieve the effects of environmental friendliness, improve brightness, and improve flatness
- Summary
- Abstract
- Description
- Claims
- Application Information
AI Technical Summary
Problems solved by technology
Method used
Image
Examples
Embodiment 1)
[0025] The present embodiment carries out alkaline chemical polishing to the surface of 7075 aluminum alloy, and has the following steps:
[0026] ① Soak the 7075 aluminum alloy in absolute ethanol for 5 minutes for pretreatment, and then wash it with deionized water.
[0027] ②Put the pretreated 7075 aluminum alloy into the alkaline chemical polishing solution, and perform alkaline chemical polishing at a temperature of 60°C for 10s.
[0028] The alkaline chemical polishing liquid of the present embodiment is the aqueous solution that is made up of the component of following concentration: sodium hydroxide 200g / L; Sodium nitrate 100g / L; Sodium acetate 200g / L; Sodium bromate 50g / L; Sodium fluoride 10g / L; copper sulfate 1g / L.
[0029] ③Put the polished 7075 aluminum alloy into dilute nitric acid for neutralization, then put it into deionized water for ultrasonic cleaning for 10 minutes, and finally take out the hot air and dry it.
[0030] The metallographic micrograph of the...
Embodiment 2~ Embodiment 5)
[0032] Each example is basically the same as Example 1, except for the composition of the alkaline chemical polishing solution, see Table 1 for details.
[0033] Table 1
[0034] Example 1 Example 2 Example 3 Example 4 Example 5 sodium hydroxide 200g / L 250g / L 200g / L 300g / L 150g / L sodium nitrate 100g / L 150g / L 100g / L 175g / L 75g / L sodium acetate 200g / L 250g / L 200g / L 300g / L 150g / L Sodium bromate 50g / L 75g / L 50g / L 100g / L 25g / L sodium fluoride 10g / L 15g / L 10g / L 17.5g / L 7.5g / L Sulfate Copper sulfate 1g / L Copper sulfate 1g / L Copper sulfate 2g / L Zinc sulfate 2g / L Nickel sulfate 1g / L
Embodiment 6)
[0036] The present embodiment carries out alkaline chemical polishing to the surface of 1060 aluminum alloy, and has the following steps:
[0037] ① Soak the 1060 aluminum alloy in absolute ethanol for 5 minutes for pretreatment, and then wash it with deionized water.
[0038] ②Put the pretreated 1060 aluminum alloy into the alkaline chemical polishing solution, and perform alkaline chemical polishing at a temperature of 50°C for 10s.
[0039] The alkaline chemical polishing liquid of the present embodiment is the aqueous solution that is made up of the component of following concentration: sodium hydroxide 250g / L; Sodium nitrate 150g / L; Sodium acetate 250g / L; Sodium bromate 75g / L; Sodium fluoride 15g / L; zinc sulfate 2g / L.
[0040] ③Put the polished 1060 aluminum alloy in dilute nitric acid for neutralization, then put it in deionized water for ultrasonic cleaning for 10 minutes, and finally take out the hot air and dry it.
[0041] The metallographic microscope photo of the...
PUM
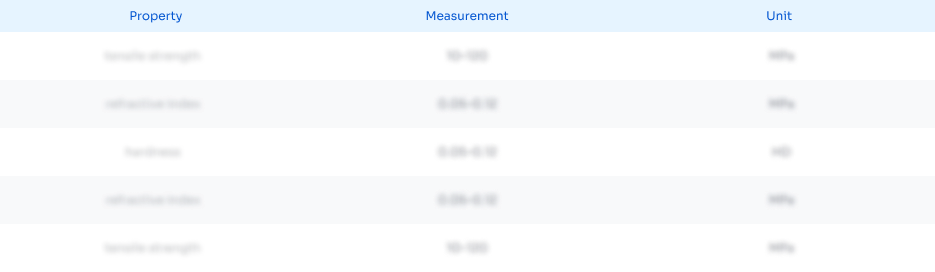
Abstract
Description
Claims
Application Information

- Generate Ideas
- Intellectual Property
- Life Sciences
- Materials
- Tech Scout
- Unparalleled Data Quality
- Higher Quality Content
- 60% Fewer Hallucinations
Browse by: Latest US Patents, China's latest patents, Technical Efficacy Thesaurus, Application Domain, Technology Topic, Popular Technical Reports.
© 2025 PatSnap. All rights reserved.Legal|Privacy policy|Modern Slavery Act Transparency Statement|Sitemap|About US| Contact US: help@patsnap.com