Calcium roasting floatation separation method for bastnaesite
A technology of bastnaesite and calcification roasting, which is applied in flotation, solid separation, etc., can solve the problems of fluorine not being utilized as resources, fluorine-containing waste water polluting the environment, complex process, etc., achieve high recovery rate of rare earth, improve economic efficiency Benefits, the effect of reducing environmental pollution
- Summary
- Abstract
- Description
- Claims
- Application Information
AI Technical Summary
Problems solved by technology
Method used
Image
Examples
Embodiment 1
[0036] The composition of the bastnaesite used contains 60% rare earth oxides in terms of REO and 7% fluorine by weight percentage;
[0037] Mix bastnaesite and calcium hydroxide uniformly according to the mass ratio of 5:1, roast at 650°C for 3 hours, and cool to normal temperature to obtain roasted ore;
[0038] Put the roasted ore in the flotation cell of the flotation machine, add water and stir to form a slurry with a concentration of 200g / L, and then adjust the pH value of the slurry to 8 with 1mol / L dilute hydrochloric acid;
[0039] Add water glass to the slurry and stir, then add sodium oxalate and stir, then add sodium oleate and stir, then add No. 2 oil and stir, the stirring time after adding each agent is 3min; 0.2g / kg bastnaesite, the addition amount of sodium oxalate is 2g / kg bastnaesite, the addition amount of sodium oleate is 0.8g / kg bastnaesite, the addition amount of No. 2 oil is 2mL / kg fluorine Carbenite; Then open the inflation valve of the flotation mach...
Embodiment 2
[0043] The composition of the bastnaesite used contains 30% rare earth oxides in terms of REO and 3% fluorine by weight percentage;
[0044] Method is with embodiment 1, and difference is:
[0045] (1) Mix bastnaesite and calcium hydroxide evenly according to the mass ratio of 3:1, and roast at 500°C for 4 hours;
[0046] (2) Add water and stir to form a pulp with a concentration of 300g / L, and then use 1mol / L sodium carbonate solution to adjust the pH value of the pulp to 10;
[0047] (3) Add water glass, potassium oxalate, sodium oleate and No. 2 oil in sequence, and the stirring time after each agent is added is 4 minutes; the amount of addition is 0.4 g / kg bastnaesite in water glass, and 3 g / kg potassium oxalate Bastnaesite, sodium oleate 0.6g / kg bastnaesite, No. 2 oil 1.5mL / kg bastnaesite;
[0048](4) Carry out 5-stage screening on the roughing tailings, the weight purity of rare earth oxides obtained is 93%, the recovery rate of rare earths reaches 92%; the recovery ra...
Embodiment 3
[0050] The composition of the bastnaesite used is 70% by weight percentage containing rare earth oxide, calculated as REO, and contains 10% fluorine;
[0051] Method is with embodiment 1, and difference is:
[0052] (1) Mix bastnaesite and calcium hydroxide evenly according to the mass ratio of 7:1, and roast at 800°C for 2 hours;
[0053] (2) Add water and stir to form a pulp with a concentration of 350g / L, and then adjust the pH value of the pulp to 7 with 1mol / L dilute hydrochloric acid;
[0054] (3) Add water glass, calcium oxalate, sodium oleate and No. 2 oil in sequence, and the stirring time after each agent is added is 5 minutes; the amount of addition is 0.6g / kg bastnaesite in water glass, and 2g / kg calcium oxalate Bastnaesite, sodium oleate 0.4g / kg bastnaesite, No. 2 oil 1mL / kg bastnaesite;
[0055] (4) Carry out 9-stage screening on the roughing tailings, the weight purity of rare earth oxides obtained is 90%, the recovery rate of rare earths reaches 95%; the reco...
PUM
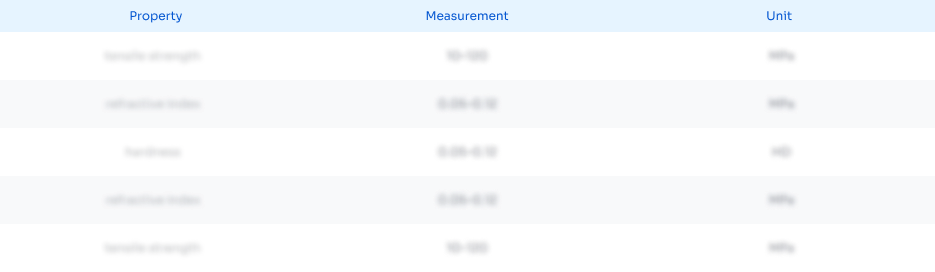
Abstract
Description
Claims
Application Information

- Generate Ideas
- Intellectual Property
- Life Sciences
- Materials
- Tech Scout
- Unparalleled Data Quality
- Higher Quality Content
- 60% Fewer Hallucinations
Browse by: Latest US Patents, China's latest patents, Technical Efficacy Thesaurus, Application Domain, Technology Topic, Popular Technical Reports.
© 2025 PatSnap. All rights reserved.Legal|Privacy policy|Modern Slavery Act Transparency Statement|Sitemap|About US| Contact US: help@patsnap.com