Method for preparing thin thermal battery negative electrode pole piece based on slurry coating method
A technology for negative electrode pole pieces and thermal batteries, which is applied in the field of preparing thin thermal battery negative pole pieces based on the slurry coating method, can solve the problems that the thermal battery pole pieces cannot be thinned, and achieve high utilization of active materials and high electrochemical performance. Improvement and small internal resistance
- Summary
- Abstract
- Description
- Claims
- Application Information
AI Technical Summary
Problems solved by technology
Method used
Examples
Embodiment 1
[0023] Preparation of thermal battery negative electrode homogeneous slurry: In a drying room with a humidity 7 h 16 80% of the organic dispersant was mixed according to the proportion, and mechanically stirred at a speed of 1500r / min for 30 minutes to obtain a uniform slurry for the negative electrode of the heated battery; the above proportions are all percentages by mass.
[0024] On the surface-treated graphite paper, a thermal battery negative electrode uniform slurry with a thickness of 50 um was coated at a speed of 45 cm / min, and was cured in a vacuum oven at 100 ° C for 30 min; Press down for 4 minutes to obtain a thin thermal battery negative electrode sheet; the thickness of the negative electrode sheet is 25um.
Embodiment 2
[0026] Preparation of homogeneous slurry for thermal battery negative electrode: In a glove box, lithium aluminum alloy Li-Al20%, PTFE emulsion binder 0.2% and C 2 h 6 O organic dispersant 79.8% was mixed according to the proportion, and the speed of 300r / min was magnetically stirred for 24 hours to obtain a uniform slurry for the negative electrode of the heated battery; the above proportions are all percentages by mass.
[0027] Then, on the surface-treated metal foil, coat a 100um-thick thermal battery negative electrode uniform slurry at a speed of 20cm / min, and dry it in a vacuum oven at 25°C for 24h; Press for 30 seconds to obtain a thin thermal battery negative pole piece; the thickness of the negative pole piece is 80um.
Embodiment 3
[0029] Preparation of homogeneous slurry for negative electrode of thermal battery: In a drying room with humidity 4 h 7 25% of the NO organic dispersant was mixed according to the ratio, and stirred magnetically at a speed of 1000r / min for 2 hours to obtain a uniform slurry for the negative electrode of the heated battery; the above ratios are all percentages by mass.
[0030] Then, on the surface-treated metal sheet, coat a 400 um thick thermal battery negative electrode uniform slurry at a speed of 5 cm / min, and dry it in a vacuum oven at 60 ° C for 10 h to cure; then prepare the sample under a pressure of 2 Mpa Press for 5 minutes to obtain a thin thermal battery negative pole piece; the thickness of the negative pole piece is 350um.
PUM
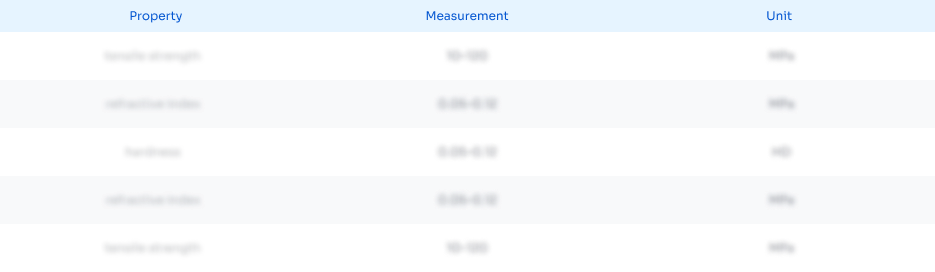
Abstract
Description
Claims
Application Information

- Generate Ideas
- Intellectual Property
- Life Sciences
- Materials
- Tech Scout
- Unparalleled Data Quality
- Higher Quality Content
- 60% Fewer Hallucinations
Browse by: Latest US Patents, China's latest patents, Technical Efficacy Thesaurus, Application Domain, Technology Topic, Popular Technical Reports.
© 2025 PatSnap. All rights reserved.Legal|Privacy policy|Modern Slavery Act Transparency Statement|Sitemap|About US| Contact US: help@patsnap.com