Preparation method of composite fiber for wig
A technology of composite fibers and wigs, which is applied in the chemical characteristics of fibers, cellulose/protein conjugated rayon, and rayon manufacturing, etc., can solve the problems of secondary burns, unsatisfactory flame retardant performance, and high energy consumption. Achieve the effect of preventing shrinkage, improving mechanical strength, and improving strength and modulus
- Summary
- Abstract
- Description
- Claims
- Application Information
AI Technical Summary
Problems solved by technology
Method used
Image
Examples
Embodiment 1
[0031] Preparation of high-strength sodium alginate / Antarctic krill protein artificial wig composite fiber:
[0032] (1) Add Antarctic krill protein to 0.2% NaOH aqueous solution, dissolve it in a constant temperature water bath at 60°C for 20 minutes, then add a composite enhancer and mix evenly, finally add sodium alginate and stir evenly, and stand in a vacuum at 25°C to remove Spinning dope obtained by brewing; wherein the percentages by weight of Antarctic krill protein, composite reinforcing agent and sodium alginate in spinning dope are 20%, 10% and 70% respectively;
[0033] (2) Place the spinning stock solution in a spinning tank at 30°C to extrude, and then put it into a calcium chloride coagulation bath with a mass percent concentration gradient of 3%, 5%, and 7% in turn to solidify into silk. The temperatures of the baths are 30°C, 40°C, and 40°C respectively, and the solidification time of the spinning stock solution in each coagulation bath is 20-30s respectively...
Embodiment 2
[0038] Preparation of high-strength sodium alginate / Antarctic krill protein artificial wig composite fiber:
[0039] (1) Add Antarctic krill protein to 2% NaOH aqueous solution, dissolve it in a constant temperature water bath at 40°C for 60 minutes, then add a composite enhancer and mix evenly, finally add sodium alginate and stir evenly, stand in a vacuum at 25°C to remove The spinning stock solution is soaked; wherein the percentages by weight of Antarctic krill protein, composite reinforcing agent and sodium alginate in the spinning stock solution are 40%, 1% and 59% respectively;
[0040] (2) Place the spinning stock solution in the spinning tank at 50°C to extrude, and then put it into the composite metal ion coagulation bath with a mass percentage concentration of 5%, 7%, and 9% to solidify into silk, and three coagulation baths The temperatures are 30°C, 40°C, and 40°C, respectively, and the solidification time of the spinning stock solution in each coagulation bath is...
Embodiment 3
[0044] Preparation of high-strength sodium alginate / Antarctic krill protein artificial wig composite fiber:
[0045] (1) Add Antarctic krill protein to 1% NaOH aqueous solution, dissolve in a constant temperature water bath at 60°C for 30 minutes, then add a composite enhancer and mix evenly, and finally add sodium alginate and stir evenly, and stand in a vacuum at 25°C to remove Spinning dope obtained by brewing; wherein the percentages by weight of Antarctic krill protein, composite reinforcing agent and sodium alginate in spinning dope are 30%, 5% and 65% respectively;
[0046] (2) Put the spinning stock solution in the spinning tank and extrude it at 40°C, put it into the composite metal ion coagulation baths with a mass percentage concentration of 3%, 5%, and 9% in turn to solidify into silk, three coagulation baths The temperatures are 30°C, 40°C, and 40°C respectively, and the solidification time of the spinning stock solution in each coagulation bath is 20-30s respecti...
PUM
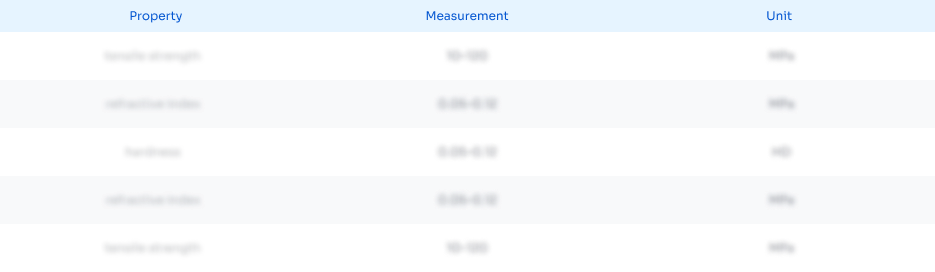
Abstract
Description
Claims
Application Information

- R&D
- Intellectual Property
- Life Sciences
- Materials
- Tech Scout
- Unparalleled Data Quality
- Higher Quality Content
- 60% Fewer Hallucinations
Browse by: Latest US Patents, China's latest patents, Technical Efficacy Thesaurus, Application Domain, Technology Topic, Popular Technical Reports.
© 2025 PatSnap. All rights reserved.Legal|Privacy policy|Modern Slavery Act Transparency Statement|Sitemap|About US| Contact US: help@patsnap.com