Method for producing MTBE from high-concentration isobutene by adopting mixed phase bed reactor
A high isobutylene and reactor technology, applied in the chemical industry, climate sustainability, organic chemistry, etc., can solve the problems of high investment in catalytic distillation technology and difficulty in catalyst loading, and achieve the effect of reducing energy consumption and equipment investment
- Summary
- Abstract
- Description
- Claims
- Application Information
AI Technical Summary
Problems solved by technology
Method used
Image
Examples
Embodiment 1
[0024] Such as figure 1 As shown, the first embodiment of the present invention provides a high-content isobutene mixed carbon four synthetic MTBE process flow.
[0025] After fully mixing the mixed C4 containing 45%wt isobutene and methanol through the mixer 101, the isobutene and methanol are mixed at a molecular ratio of 1:0.8, heated to 40°C by the feed pre-heater 102, and mixed with the circulating material to enter the mixed phase Bed reactor 103, wherein the isobutene content in the inlet raw material is 14.2wt%. The mixed-phase bed reactor is a cylinder reactor, and the material passes through the catalytic bed layer from bottom to top, and the operating pressure is controlled at 650kPaG. In the mixed-phase bed reactor, the heat released by the reaction vaporizes part of the materials, the vaporization rate is controlled at 13.7%, and the reactor outlet temperature is 65.2°C. The reacted gas-liquid mixture enters the flash tank 104 for gas-liquid separation, wherein ...
Embodiment 2
[0027] The isobutene and methanol in the raw carbon four are mixed at a molecular ratio of 1:0.85. The isobutene content in the raw material at the reactor inlet was 12.6wt%, the reaction pressure was controlled at 650kPaG, the reactor outlet temperature was 64.5°C, and the vaporization rate was 9.9%. The flow rate of the circulating material is controlled at 60% of the flow rate of the C4 raw material, and the temperature of the circulating material after cooling is 40°C. The reflux ratio of the catalytic distillation tower is 0.7, and the top pressure of the catalytic distillation tower is 500kPaG. All the other are with embodiment 1.
[0028] It has been determined that the energy consumption of the catalytic rectification tower using the mixed-phase bed process is 13.1MW, and the MTBE purity in the bottom of the tower is 99.53%.
Embodiment 3
[0030] The isobutene and methanol in the raw carbon four are mixed at a molecular ratio of 1:0.9. The isobutene content in the raw material at the reactor inlet was 15.4 wt%, the reaction pressure was controlled at 700kPaG, the reactor outlet temperature was 68.2°C, and the vaporization rate was 14.2%. The flow rate of the circulating material is controlled at 50% of the flow rate of the C4 raw material. The temperature of the circulating material after cooling is 40°C. The reflux ratio of the catalytic distillation tower is 0.8, and the top pressure of the catalytic distillation tower is 550kPaG. All the other are with embodiment 1.
[0031] It has been determined that the energy consumption of the catalytic rectification tower using the mixed-phase bed process is 13.2MW, and the MTBE purity in the bottom of the tower is 99.55%.
PUM
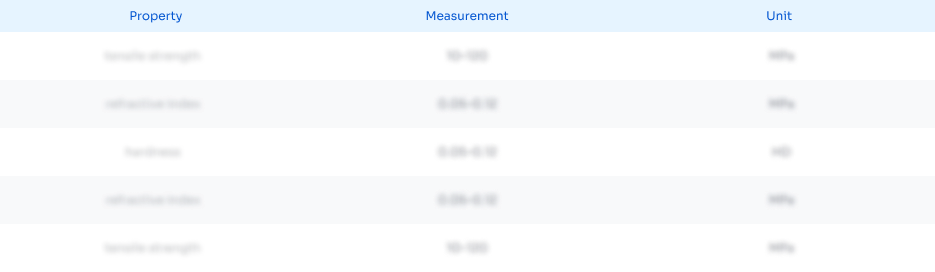
Abstract
Description
Claims
Application Information

- Generate Ideas
- Intellectual Property
- Life Sciences
- Materials
- Tech Scout
- Unparalleled Data Quality
- Higher Quality Content
- 60% Fewer Hallucinations
Browse by: Latest US Patents, China's latest patents, Technical Efficacy Thesaurus, Application Domain, Technology Topic, Popular Technical Reports.
© 2025 PatSnap. All rights reserved.Legal|Privacy policy|Modern Slavery Act Transparency Statement|Sitemap|About US| Contact US: help@patsnap.com