Same-direction rotary-floating smelting method, nozzle and metallurgical equipment
A nozzle and cyclone technology, which is used in the field of metal sulfide concentrate powder to obtain sulfur and even metal products, can solve the problem of large differences in physical specifications, specific gravity and chemical composition properties, the inability of concentrate particles to be oxidized, and the difficulty of swirl strength. Control and other problems, to achieve the effect of no reaction dead zone, small reaction space, and large production capacity
- Summary
- Abstract
- Description
- Claims
- Application Information
AI Technical Summary
Problems solved by technology
Method used
Image
Examples
Embodiment Construction
[0035] The invention discloses a new co-rotating flotation smelting method to improve the utilization rate of oxygen and make the material react with oxygen completely; it overcomes the flashing phenomenon of the swirling flow and the reflux phenomenon of a large amount of high-temperature flue gas in the outer ring, and the required The reaction space is small, there is no reaction dead zone, and the erosion of the refractory material of the furnace body is small. The invention provides a co-rotating buoyant smelting nozzle for realizing the above method, and a metallurgical equipment using the above nozzle.
[0036] The following will clearly and completely describe the technical solutions in the embodiments of the present invention with reference to the accompanying drawings in the embodiments of the present invention. Obviously, the described embodiments are only some, not all, embodiments of the present invention. Based on the embodiments of the present invention, all oth...
PUM
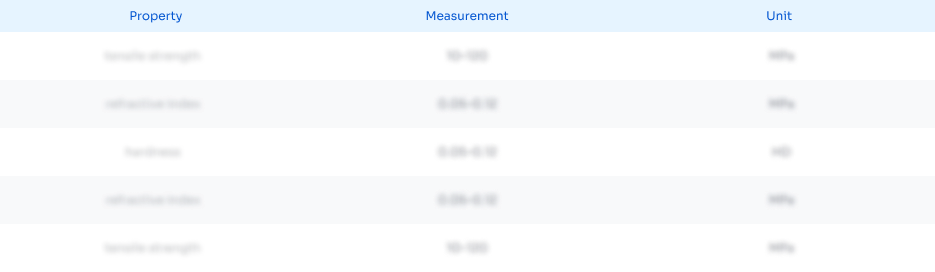
Abstract
Description
Claims
Application Information

- R&D
- Intellectual Property
- Life Sciences
- Materials
- Tech Scout
- Unparalleled Data Quality
- Higher Quality Content
- 60% Fewer Hallucinations
Browse by: Latest US Patents, China's latest patents, Technical Efficacy Thesaurus, Application Domain, Technology Topic, Popular Technical Reports.
© 2025 PatSnap. All rights reserved.Legal|Privacy policy|Modern Slavery Act Transparency Statement|Sitemap|About US| Contact US: help@patsnap.com