Environmentally-friendly plastic thrust bearing bush and production method thereof
A technology of thrust bearing bushes and environmentally friendly plastics, which is applied in the direction of bearing components, shafts and bearings, mechanical equipment, etc., can solve the problems of lead environmental pollution and other problems, and achieve the effects of fast molding cycle, high dimensional stability, and outstanding environmental protection performance
- Summary
- Abstract
- Description
- Claims
- Application Information
AI Technical Summary
Problems solved by technology
Method used
Examples
Embodiment 1
[0028] The polyetheretherketone plate comprises the following components by weight percentage: 500g of polyetheretherketone resin.
[0029] The manufacturing method of the new environment-friendly plastic thrust bearing bush:
[0030] (1) Put 500g of polyether ether ketone resin into a mold, and hot press molding on a hot press, with a molding temperature of 370°C and a molding pressure of 20MPa, to obtain a polyether ether ketone sheet;
[0031] (2) Mix the environment-friendly epoxy adhesive and curing agent according to the ratio requirements, and stir evenly;
[0032] (3) Apply epoxy adhesive evenly on the steel tile base and the polyetheretherketone board, and remove oil stains and other impurities on the steel tile base and the modified polyetheretherketone board with acetone or other solvents before applying the glue;
[0033] (4) Cover the polyether ether ketone plate coated with adhesive on the steel tile base, put it into a hydraulic press, the molding temperature i...
Embodiment 2
[0036] The polyetheretherketone plate comprises the following components by weight percentage: 400g of polyetheretherketone resin, 85g of a mixture of carbon fiber and glass fiber, and 15g of a mixture of graphite and molybdenum disulfide.
[0037] The manufacturing method of the new environment-friendly plastic thrust bearing bush:
[0038] (1) Add carbon fiber, glass fiber, graphite, and molybdenum disulfide to polyether ether ketone resin, stir to distribute the filler evenly, then put it into a mold, and press it on a hot press for molding. The molding temperature is 380°C and the molding pressure is 20MPa, to obtain polyether ether ketone plate;
[0039] (2) Mix the environment-friendly polyurethane adhesive and curing agent according to the ratio requirements, and stir evenly;
[0040] (3) Apply polyurethane adhesive evenly on the steel tile base and PEEK board, and remove oil stains and other impurities on the steel tile base and PEEK board with acetone or other solven...
Embodiment 3
[0044] The polyetheretherketone plate comprises the following components by weight percentage: 400g of polyetheretherketone resin, 85g of a mixture of carbon fiber and glass fiber, and 15g of a mixture of graphite and molybdenum disulfide.
[0045] The manufacturing method of the new environment-friendly plastic thrust bearing bush:
[0046] (1) Add carbon fiber, glass fiber, graphite, and molybdenum disulfide to polyether ether ketone resin, stir to distribute the filler evenly, then put it into a mold, and press it on a hot press for molding. The molding temperature is 380°C and the molding pressure is 20MPa, to obtain polyether ether ketone plate;
[0047] (2) Mix the environment-friendly epoxy adhesive and curing agent according to the ratio requirements, and stir evenly;
[0048] (3) Apply epoxy adhesive evenly on the steel tile base and PEEK board, and remove oil stains and other impurities on the steel tile base and PEEK board with acetone or other solvents before appl...
PUM
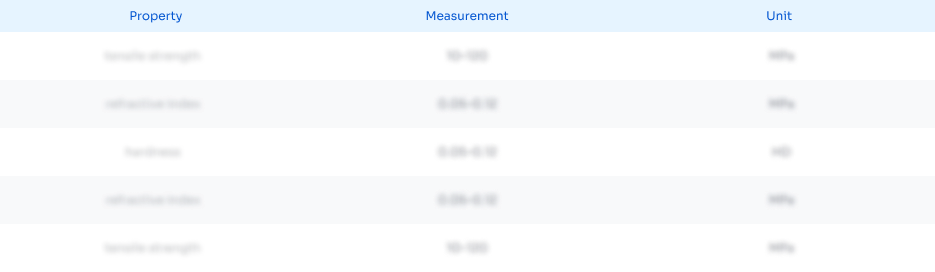
Abstract
Description
Claims
Application Information

- R&D
- Intellectual Property
- Life Sciences
- Materials
- Tech Scout
- Unparalleled Data Quality
- Higher Quality Content
- 60% Fewer Hallucinations
Browse by: Latest US Patents, China's latest patents, Technical Efficacy Thesaurus, Application Domain, Technology Topic, Popular Technical Reports.
© 2025 PatSnap. All rights reserved.Legal|Privacy policy|Modern Slavery Act Transparency Statement|Sitemap|About US| Contact US: help@patsnap.com