Preparation method for nano additive
A technology of nano-additives and dispersants, applied in textiles and papermaking, fiber treatment, fiber types, etc., can solve problems such as the increase of volatile substances, environmental impact, etc., and achieve the effect of increasing antibacterial properties
- Summary
- Abstract
- Description
- Claims
- Application Information
AI Technical Summary
Problems solved by technology
Method used
Image
Examples
Embodiment 1
[0014] The present embodiment provides a kind of preparation method of nano-additive. The preparation steps of described nano-additive are as follows:
[0015] Step 1: First, add 5 parts of zinc oxide, 3 parts of titanium dioxide, and 0.5 parts of dispersant into the ball mill at a speed of 350 rpm, and grind for 8 hours to obtain dry powder A
[0016] Step 2: Mix dry powder A according to the ratio of 1g dry powder to 5ml ethanol, add it to a ball mill, continue grinding, adjust the speed to 480 rpm, ball mill for 5 hours, remove absolute ethanol, and vacuum dry to obtain nano dry powder B
[0017] Step 3: Add 2 parts of montmorillonite and 3 parts of vermiculite together with 0.5 parts of dispersant to absolute ethanol. The content of inorganic mineral salts in this mixture is 40-60%. Put this mixture into an ultrasonic field for ultrasonic dispersion and stripping for 3 hours , after dispersing, remove the ethanol, together with the dry powder B, continue to add to the ball...
Embodiment 2
[0019] The present embodiment provides a kind of preparation method of nano-additive. The preparation steps of described nano-additive are as follows:
[0020] Step 1: First, add 10 parts of zinc oxide, 5 parts of titanium dioxide, and 1.5 parts of dispersant into the ball mill at a speed of 350 rpm, and grind for 7 hours to obtain dry powder A
[0021] Step 2: Mix dry powder A according to the ratio of 1g dry powder to 5ml ethanol, add it to a ball mill, continue grinding, adjust the speed to 480 rpm, ball mill for 5 hours, remove absolute ethanol, and vacuum dry to obtain nano dry powder B
[0022] Step 3: Add 6 parts of montmorillonite and 6 parts of vermiculite together with 1.5 parts of dispersant to absolute ethanol. The content of inorganic mineral salt in this mixture is 40-60%. Put this mixture into an ultrasonic field for ultrasonic dispersion and stripping 2.5 h, after dispersing, remove the ethanol, and continue to add the dry powder B into a ball mill at 600 rpm f...
Embodiment 3
[0024] The present embodiment provides a kind of preparation method of nano-additive. The preparation steps of described nano-additive are as follows:
[0025] Step 1: First, add 7 parts of zinc oxide, 4 parts of titanium dioxide, and 1.5 parts of dispersant into the ball mill at a speed of 350 rpm, and grind for 6 hours to obtain dry powder A
[0026] Step 2: Mix dry powder A according to the ratio of 1g of dry powder to 5ml of ethanol, add it to a ball mill, continue grinding, adjust the speed to 450 rpm, ball mill for 5.5 hours, remove absolute ethanol, and vacuum dry to obtain nano dry powder B
[0027] Step 3: Add 4 parts of montmorillonite and 2 parts of vermiculite together with 1.5 parts of dispersant to absolute ethanol. The content of inorganic mineral salt in this mixture is 40-60%. Put this mixture into an ultrasonic field for ultrasonic dispersion and stripping for 3 hours , after dispersion, remove ethanol, together with dry powder B, continue to add to the ball ...
PUM
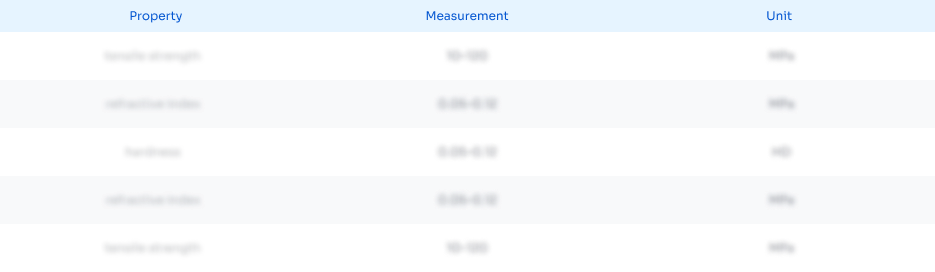
Abstract
Description
Claims
Application Information

- R&D
- Intellectual Property
- Life Sciences
- Materials
- Tech Scout
- Unparalleled Data Quality
- Higher Quality Content
- 60% Fewer Hallucinations
Browse by: Latest US Patents, China's latest patents, Technical Efficacy Thesaurus, Application Domain, Technology Topic, Popular Technical Reports.
© 2025 PatSnap. All rights reserved.Legal|Privacy policy|Modern Slavery Act Transparency Statement|Sitemap|About US| Contact US: help@patsnap.com