Method for producing ferrochrome
A ferrochromium alloy and production process technology, which is applied in the field of producing ferrochromium alloy by grate machine-rotary kiln combined metallized pellet hot charging, can solve the problem of inability to produce ferrochromium alloy lumps, etc., and achieves reduction of power consumption and cost, and improvement of work efficiency. Efficiency, the effect of overcoming pollution
- Summary
- Abstract
- Description
- Claims
- Application Information
AI Technical Summary
Problems solved by technology
Method used
Image
Examples
Embodiment 1
[0036] First, 16% of coke powder, 2.5% of bentonite, and the balance of chrome ore are used in the mixed batching, and the SiO in the batching is controlled. 2The weight ratio of MgO is 2.5%, and the weight ratio of MgO is 8%; the dried mixed ingredients are ball milled to -0.074mm, which is greater than 90%, and then sprayed with water and mixed until the weight moisture content of the mixture is 12%, and then heated at room temperature After waking up for 3 hours, make pellets, the particle size of the pellets is Φ16±2mm; the pellets are dried and preheated with a grate machine, the drying temperature is 40°C, and the drying time is 30 minutes. The waste heat is returned to the drying process of the mixed ingredients; then the rotary kiln pellet pre-reduction process is carried out. The pre-reduction process is to use the rotary kiln for pellet pre-reduction. The reduction rate of chromium is controlled at 50%, the reduction temperature is 1350 ° C, and the reduction time is ...
Embodiment 2
[0038] First, 20% of coke powder, 4% of bentonite, and the balance of chromium ore are mixed in the weight ratio, and the SiO in the batch is controlled. 2 The weight ratio of MgO is 7%, and the weight ratio of MgO is 14%; the dried mixed ingredients are ball-milled to -0.074mm, which is greater than 90%, and then sprayed with water and mixed until the weight moisture content of the mixture is 15%, and then heated at room temperature After waking up for 9 hours, make pellets, and the particle size of the pellets is Φ16±2mm; the pellets are dried and preheated with a grate machine, and the drying temperature is 900°C, and the drying time is 10 minutes. The waste heat is returned to the drying process of the mixed ingredients; then the rotary kiln pellet pre-reduction process is carried out. The pre-reduction process is to use the rotary kiln for pellet pre-reduction. The reduction rate of chromium is controlled at 55%, the reduction temperature is 1400 ° C, and the reduction tim...
Embodiment 3
[0040] First, 24% of coke powder, 5% of bentonite, and the balance of chrome ore are mixed in the weight ratio, and the SiO in the batch is controlled. 2 The weight ratio of MgO is 8%, and the weight ratio of MgO is 16%; the dried mixed ingredients are ball-milled to -0.074mm, which is greater than 90%, and then sprayed with water and mixed until the weight moisture content of the mixture is 15%, and then heated at room temperature After waking up the material for more than 10 hours, pelletize, and the particle size of the pellets is Φ16±2mm; the pellets are dried and preheated with a grate machine, and the drying temperature is 600°C for 18 minutes, and the drying preheating process produces The residual heat is returned to the drying process of the mixed ingredients; then the rotary kiln pellet pre-reduction process is carried out. The pre-reduction process is to use the rotary kiln for pellet pre-reduction. The reduction rate of chromium is controlled at 65%, the reduction t...
PUM
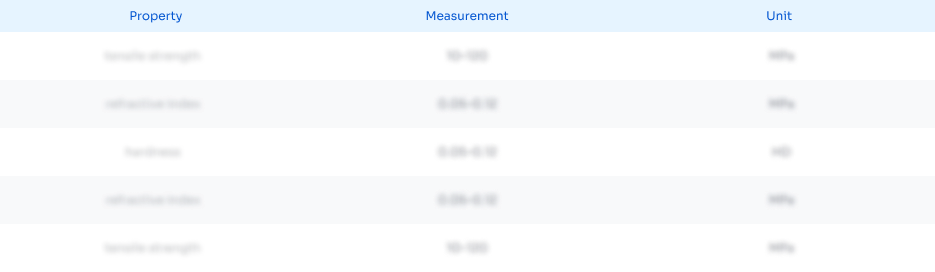
Abstract
Description
Claims
Application Information

- Generate Ideas
- Intellectual Property
- Life Sciences
- Materials
- Tech Scout
- Unparalleled Data Quality
- Higher Quality Content
- 60% Fewer Hallucinations
Browse by: Latest US Patents, China's latest patents, Technical Efficacy Thesaurus, Application Domain, Technology Topic, Popular Technical Reports.
© 2025 PatSnap. All rights reserved.Legal|Privacy policy|Modern Slavery Act Transparency Statement|Sitemap|About US| Contact US: help@patsnap.com