Industrial production method and device for highly isotactic polybutylene alloy
A technology for producing high-tactic polybutene and a production device, which is applied in the petrochemical field, can solve problems such as unseen methods, steps and device disclosure, and achieve the effects of filling market gaps, no three-waste emissions, and simple preparation methods.
- Summary
- Abstract
- Description
- Claims
- Application Information
AI Technical Summary
Problems solved by technology
Method used
Image
Examples
Embodiment 1
[0052] After the prepolymerization kettle of 3 cubic meters is processed by the vacuum nitrogen system, the triethylaluminum (Al) and the external electron donor methylcyclohexyldimethoxysilane ( Silicon Si compound) and supported titanium catalyst (Ti mass content 3.5%) 200g, then add 1000Kg of refined propylene, wherein Al / Ti=20 (molar ratio), Al / Si=0.5 (molar ratio). Stir and polymerize at 90°C for 3 hours, depressurize the prepolymerization tank through a decompression device, and discharge the unreacted propylene monomer into the propylene monomer gas cabinet. The polypropylene particles after removal of propylene are transported through the pipeline system to a 12 cubic meter polymerization kettle treated by a vacuum nitrogen system, and then 3000Kg of refined liquid phase 1-butene monomer is added to the polymerization kettle through the batching system, Add 10 L of hydrogen gas and react at 30°C for 8 hours. After the reaction, the polymerization tank is decompressed t...
Embodiment 2
[0054] After the 3 cubic meters of prepolymerization kettle is treated by vacuum nitrogen system, metered monomethylaluminum dichloride (Al), external electron donor diisopropyldimethoxy Base silane (silicon Si compound) and supported titanium catalyst (Ti mass content 2%) 180g, then add propylene 1000Kg after refining, wherein Al / Ti=200 (molar ratio), Al / Si=0.001 (molar ratio). Stir and polymerize at 60°C for 6 hours, depressurize the prepolymerization tank through a decompression device, and discharge unreacted propylene monomer into the propylene monomer gas tank. The polypropylene particles after removal of propylene are transported through the pipeline system to a 12 cubic meter polymerization kettle treated by a vacuum nitrogen system, and then 1500Kg of refined liquid-phase 1-butene monomer is added to the polymerization kettle through the batching system, Add 15 L of hydrogen gas, and react at -10°C for 48 hours. After the reaction, the polymerization tank is decompres...
Embodiment 3
[0056] After the 3 cubic meter prepolymerization kettle is treated by the vacuum nitrogen system, the metered dimethylaluminum monochloride (Al), the external electron donor dicyclopentadimethoxy Silane (silicon Si compound) and supported titanium catalyst (Ti mass content 3.3%) 180g, then add 600Kg of refined propylene, wherein Al / Ti=10 (molar ratio), Al / Si=0.01 (molar ratio). Stir and polymerize at -20°C for 0.1 h, depressurize the prepolymerization tank through a decompression device, and discharge the unreacted propylene monomer into the propylene monomer gas tank. The polypropylene particles after removal of propylene are transported through the pipeline system to a 12 cubic meter polymerization kettle treated by a vacuum nitrogen system, and then 3000Kg of refined liquid phase 1-butene monomer is added to the polymerization kettle through the batching system, Add 16L of hydrogen gas and react at 30°C for 8 hours. After the reaction, the polymerization tank is decompresse...
PUM
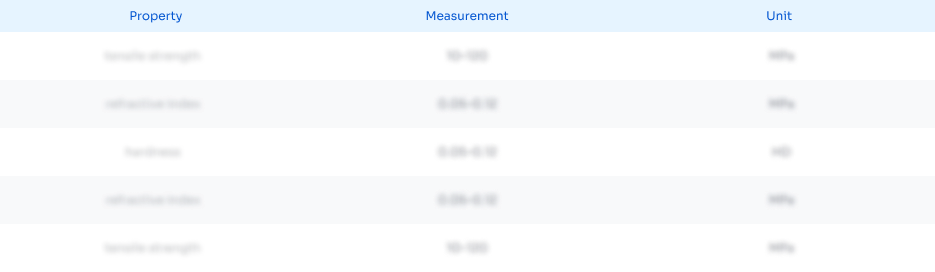
Abstract
Description
Claims
Application Information

- Generate Ideas
- Intellectual Property
- Life Sciences
- Materials
- Tech Scout
- Unparalleled Data Quality
- Higher Quality Content
- 60% Fewer Hallucinations
Browse by: Latest US Patents, China's latest patents, Technical Efficacy Thesaurus, Application Domain, Technology Topic, Popular Technical Reports.
© 2025 PatSnap. All rights reserved.Legal|Privacy policy|Modern Slavery Act Transparency Statement|Sitemap|About US| Contact US: help@patsnap.com