Epoxy resin composition, preparation method of epoxy resin composition and composite material for wind power blade
An epoxy resin and composite material technology, applied in the field of wind power blade materials, can solve the problems of few active functional groups, long operating time, and short operating time.
- Summary
- Abstract
- Description
- Claims
- Application Information
AI Technical Summary
Problems solved by technology
Method used
Image
Examples
Embodiment 1
[0075] Embodiment 1: the preparation of epoxy resin composition of the present invention
[0076] (1) Take by weighing 60 parts of E-54 type bisphenol A epoxy resin and 40 parts of 1,4-butanediol diglycidyl ether according to the parts by weight of each component in the component (A), the E-54 Add type bisphenol A epoxy resin into the reaction kettle, heat with temperature control, and the heating temperature is 70°C; then add 1,4-butanediol diglycidyl ether, stir for 30 minutes, evacuate until the vacuum degree is equal to 80mbar, and remove Bubbles, continue to stir for 2 hours to make the mixture uniform, stop stirring after breaking the vacuum with nitrogen, and let stand for 0.5 hours to obtain component (A), sealed and preserved;
[0077] (2) Weigh 70 parts of T403 polyetheramine, 10 parts of N-aminoethylpiperazine and 20 parts of 3,3-dimethyl-4,4 according to the parts by weight of each component in component (B). -Diamino-dicyclohexylmethane, add T403 type polyetheram...
Embodiment 2
[0080] Embodiment 2: the preparation of epoxy resin composition of the present invention
[0081] (1) Take by weighing 95 parts of E-51 type bisphenol A epoxy resin and 5 parts of 1,4-butanediol diglycidyl ether according to the parts by weight of each component in component (A), and E-51 Add type bisphenol A epoxy resin into the reaction kettle, heat with temperature control, and the heating temperature is 60°C; then add 1,4-butanediol diglycidyl ether, stir for 30 minutes, evacuate until the vacuum degree is equal to 70mbar, and remove Bubbles, continue to stir for 2 hours to make the mixture uniform, stop stirring after breaking the vacuum with nitrogen, and let stand for 0.5 hours to obtain component (A), sealed and preserved;
[0082] (2) Weigh 50 parts of D403 type polyetheramine, 20 parts of 1,3-bis(aminomethyl)cyclohexane and 30 parts of 4,4-dicyclohexane according to the parts by weight of each component in component (B). Amino-dicyclohexylmethane, add D403 type poly...
Embodiment 3
[0085] Embodiment 3: the preparation of epoxy resin composition of the present invention
[0086](1) Take by weighing 60 parts of E-44 type bisphenol A epoxy resin and 40 parts of 1,6-hexanediol diglycidyl ether according to the parts by weight of each component in the component (A), the E-44 Add type bisphenol A epoxy resin into the reaction kettle, heat with temperature control, and the heating temperature is 70°C; then add 1,6-hexanediol diglycidyl ether, stir for 25 minutes, evacuate until the vacuum degree is equal to 60mbar, and remove Bubbles, continue to stir for 2 hours to make the mixture uniform, stop stirring after breaking the vacuum with nitrogen, and let stand for 0.8 hours to obtain component (A), sealed and preserved;
[0087] (2) Weigh 50 parts of D400 type polyether amine, 15 parts of isophorone diamine and 35 parts of 3,3-dimethyl-4,4- Diamino-dicyclohexylmethane, add D400 type polyetheramine, isophorone diamine and 3,3-dimethyl-4,4-diamino-dicyclohexylmet...
PUM
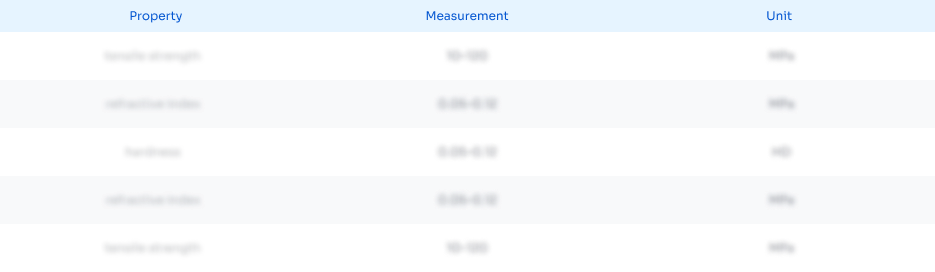
Abstract
Description
Claims
Application Information

- R&D Engineer
- R&D Manager
- IP Professional
- Industry Leading Data Capabilities
- Powerful AI technology
- Patent DNA Extraction
Browse by: Latest US Patents, China's latest patents, Technical Efficacy Thesaurus, Application Domain, Technology Topic, Popular Technical Reports.
© 2024 PatSnap. All rights reserved.Legal|Privacy policy|Modern Slavery Act Transparency Statement|Sitemap|About US| Contact US: help@patsnap.com