Hydraulic valve bonnet manufacturing process
A manufacturing process and technology for hydraulic valves, applied in valve devices and other directions, can solve problems such as easy oil leakage, high cost, and reduced mechanical properties, and achieve the effects of stable dimensional accuracy, high mechanical strength, and reduced probability of oil leakage.
- Summary
- Abstract
- Description
- Claims
- Application Information
AI Technical Summary
Problems solved by technology
Method used
Image
Examples
Embodiment Construction
[0037] The present invention is described in further detail now in conjunction with accompanying drawing. These drawings are all simplified schematic diagrams, which only illustrate the basic structure of the present invention in a schematic manner, so they only show the configurations related to the present invention.
[0038] Such as Figure 3-11 Shown, a kind of hydraulic valve bonnet manufacturing process of the present invention, comprises steps as follows,
[0039] a. Cutting: Prepare the required raw materials according to the weight and size, specifically, cut the 45# hot-rolled round bar into raw materials.
[0040] b. Heating: The raw materials are heated in a heating furnace, the temperature in the heating furnace is 1050-1100°C, and the heating furnace is an intermediate frequency induction heating furnace.
[0041] c. Upsetting: Put the heated raw material into the upsetting mold for upsetting to form a blank, and remove the oxide skin on the surface of the blan...
PUM
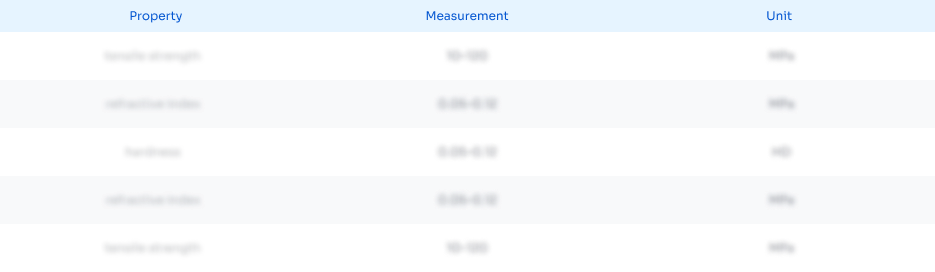
Abstract
Description
Claims
Application Information

- R&D
- Intellectual Property
- Life Sciences
- Materials
- Tech Scout
- Unparalleled Data Quality
- Higher Quality Content
- 60% Fewer Hallucinations
Browse by: Latest US Patents, China's latest patents, Technical Efficacy Thesaurus, Application Domain, Technology Topic, Popular Technical Reports.
© 2025 PatSnap. All rights reserved.Legal|Privacy policy|Modern Slavery Act Transparency Statement|Sitemap|About US| Contact US: help@patsnap.com