A preparing method of a perfluorosulfonic acid-carboxylic acid composite membrane by multilayer solution tape casting
A technology of perfluorosulfonic acid and perfluorocarboxylic acid, which is applied in the field of polymer material processing, can solve the problems of foaming and peeling of the composite film layer, the difference of the ion migration number is too large, and the resin solution is difficult to enter, so as to prolong the service life. , The effect of high process controllability and stable product quality
- Summary
- Abstract
- Description
- Claims
- Application Information
AI Technical Summary
Problems solved by technology
Method used
Examples
Embodiment 1
[0030] Weigh 150g of perfluorosulfonic acid resin particles, soak in 20% sodium hydroxide aqueous solution, and keep the temperature in a constant temperature drying oven at 100°C for 24h to make the -SO in the resin 2 The F group is completely converted to -SO 3 Na group. The transformed Na-type perfluorinated ion exchange resin is fully washed with deionized water to neutrality, and then the resin is dried in an oven for use. Put the dried perfluorosulfonic acid resin into an autoclave, add 1000ml of 1:1 isopropanol aqueous solution, heat up to 250°C, stir with magnetic force at 120r / min, and keep constant temperature and pressure for 4h. After stopping heating and stirring, naturally cool to room temperature. Take the material from the kettle to obtain a colorless transparent liquid; add 400ml of N-N dimethylformamide to the dissolved perfluorosulfonic acid solution, put it in an oven, remove isopropanol at high temperature, and wait for the low boiling point solvent to r...
Embodiment 2
[0032] Weigh 150g of perfluorosulfonic acid resin particles, soak in 20% sodium hydroxide aqueous solution, and keep the temperature in a constant temperature drying oven at 100°C for 24h to make the -SO in the resin 2 The F group is completely converted to -SO 3 Na group. The transformed Na-type perfluorinated ion exchange resin is fully washed with deionized water to neutrality, and then the resin is dried in an oven for use. Take the dried perfluorosulfonic acid resin and put it into an autoclave, add 1000ml of 1:1 isopropanol aqueous solution, heat up to 250°C, stir with magnetic force at 120r / min, and keep constant temperature and pressure for 4h. After stopping heating and stirring, cool down to room temperature naturally. Take the material from the kettle to obtain a colorless transparent liquid; add 400ml of dimethyl sulfoxide to the dissolved perfluorosulfonic acid solution, put it in an oven, remove isopropanol at high temperature, and wait for the low boiling poin...
Embodiment 3
[0034] Weigh 150g of perfluorosulfonic acid resin particles, soak in 20% sodium hydroxide aqueous solution, and keep the temperature in a constant temperature drying oven at 100°C for 24h to make the -SO in the resin 2 The F group is completely converted to -SO 3 Na group. The transformed Na-type perfluorinated ion exchange resin is fully washed with deionized water to neutrality, and then the resin is dried in an oven for use. Put the dried perfluorosulfonic acid resin into the autoclave, add 1000ml of 1:1 isopropanol aqueous solution, raise the temperature to 250°C2, stir with magnetic force at 120r / min, keep constant temperature and pressure for 4h. After stopping heating and stirring, cool down to room temperature naturally. Open the kettle and take the material to obtain a colorless transparent liquid; add 400ml of 1-methyl-2-11 pyrrolidone (NMP) to the dissolved perfluorosulfonic acid solution, put it in an oven, and remove it at high temperature. Isopropanol, after r...
PUM
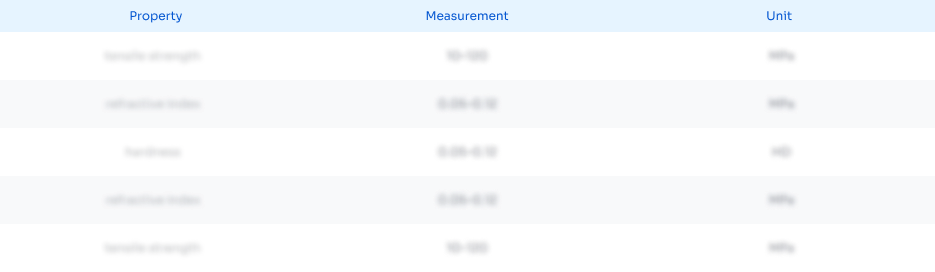
Abstract
Description
Claims
Application Information

- R&D
- Intellectual Property
- Life Sciences
- Materials
- Tech Scout
- Unparalleled Data Quality
- Higher Quality Content
- 60% Fewer Hallucinations
Browse by: Latest US Patents, China's latest patents, Technical Efficacy Thesaurus, Application Domain, Technology Topic, Popular Technical Reports.
© 2025 PatSnap. All rights reserved.Legal|Privacy policy|Modern Slavery Act Transparency Statement|Sitemap|About US| Contact US: help@patsnap.com