A kind of regeneration method of dehydrogenation catalyst
A dehydrogenation catalyst and catalyst technology, applied in chemical instruments and methods, physical/chemical process catalysts, metal/metal oxide/metal hydroxide catalysts, etc., can solve the problem of increased sintering of active centers and difficult recovery of active centers And other issues
- Summary
- Abstract
- Description
- Claims
- Application Information
AI Technical Summary
Problems solved by technology
Method used
Image
Examples
Embodiment 1
[0022] (1) Carrier preparation
[0023] Weigh 66.0g of pseudo-boehmite and 2.64g of bentonite to make a small spherical carrier through thorough mixing and kneading. The wet catalyst was dried in the air overnight, and dried at 120°C for 4 hours, and the dried sample was placed in a high-temperature furnace, raised to 600°C, and roasted at a constant temperature for 4 hours. prepared as a carrier;
[0024] (2) Formulated to 18.0% (weight concentration) Cr(NO 3 ) 3 aqueous solution;
[0025] (3) Prepare 3.86% (weight concentration) of KNO 3 aqueous solution;
[0026] (4) Take 86.80g of Cr(NO 3 ) 3 Aqueous solution, step (1) Immerse with the prepared carrier for 40 minutes, then dry at 120°C for 3 hours, and roast at a constant temperature of 580°C for 6 hours;
[0027] (5) Take 21.84g of KNO prepared in step (3) 3 Catalyst A was prepared by immersing in aqueous solution for 40 minutes, drying at 120°C for 3 hours, and roasting at 650°C for 4 hours.
Embodiment 2
[0029] (1) Prepare 3.86% (weight concentration) of KNO 3 aqueous solution.
[0030] (2) Formulated to 18.0% (weight concentration) Cr(NO 3 ) 3 aqueous solution.
[0031] (3) Combine 66.00g of pseudoboehmite, 2.64g of bentonite and 21.84g of KNO prepared in step (1) 3 The aqueous solution is fully mixed, kneaded, made into a plastic body and extruded into small balls. Then, it was dried at 120°C for 3 hours, and the dried sample was placed in a high-temperature furnace, and fired at a constant temperature of 580°C for 4 hours. Made of alumina carrier containing additives.
[0032] (4) Take 86.80g of Cr(NO 3 ) 3 The aqueous solution was used to impregnate the carrier prepared in step (4) for 40 minutes, then dried at 120°C for 3 hours, and then calcined at 650°C for 6 hours to prepare catalyst B.
Embodiment 3
[0034] The catalyst prepared in Example 1 is used in isobutane dehydrogenation to produce isobutene, dehydrogenation reaction conditions: reaction temperature 600°C, reaction space velocity 1000h -1 , the reaction pressure is normal pressure, the reaction time is 25min, and the deactivated catalyst A1 is obtained.
[0035] The catalyst prepared in Example 2 is used in isobutane dehydrogenation to produce isobutene, dehydrogenation reaction conditions: reaction temperature 600°C, reaction space velocity 1000h -1 , the reaction pressure is normal pressure, the reaction time is 25min, and the deactivated catalyst B1 is obtained.
PUM
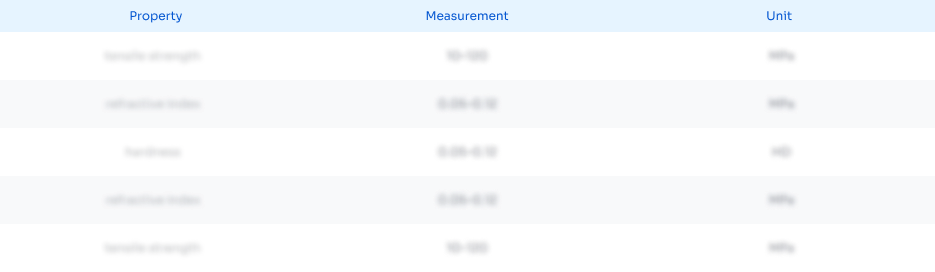
Abstract
Description
Claims
Application Information

- R&D
- Intellectual Property
- Life Sciences
- Materials
- Tech Scout
- Unparalleled Data Quality
- Higher Quality Content
- 60% Fewer Hallucinations
Browse by: Latest US Patents, China's latest patents, Technical Efficacy Thesaurus, Application Domain, Technology Topic, Popular Technical Reports.
© 2025 PatSnap. All rights reserved.Legal|Privacy policy|Modern Slavery Act Transparency Statement|Sitemap|About US| Contact US: help@patsnap.com