Method for forecasting ash fusion point variation trend after coal and sludge combined firing
A technology of changing trends and mixed combustion, which is applied in the direction of chemical analysis, instruments, and calculations by means of combustion. It can solve problems that affect the combustion effect of boiler life, difficult to predict ash melting characteristics, and boiler slagging, so as to achieve less quality and shorter prediction period. Short, less work-intensive effect
- Summary
- Abstract
- Description
- Claims
- Application Information
AI Technical Summary
Problems solved by technology
Method used
Image
Examples
Embodiment 1
[0024] Coal A and sludge sample B were dried, shrunk, ground, and sieved, and kept in an oven at 105-110°C for 2-2.5 hours to obtain a dry base sample. Chemical method, in a muffle furnace controlled by a program, burn the sample at a temperature of (815±10)°C until the quality is constant to obtain ash samples, and analyze the ash components of the ash samples, and the ash component analysis uses AXIOSadvanced wavelength dispersive X-rays Fluorescence spectrometer, the results of each mineral component of the ash component analysis are shown in the following table:
[0025] Table 1 Contents of mineral components
[0026]
[0027] From Table 1, in the mixed sample obtained from coal A and sludge B, the mineral composition Fe 2 o 3 、Al 2 o 3 and SiO 2 The contents accounted for 72.01%, 43.77% and 55.48% of the mixed samples respectively, it can be considered that Fe 2 o 3 -Al 2 o 3 -SiO 2 The component system is the main component; select Fe through the ternary pha...
Embodiment 2
[0030] Coal A and sludge sample C were dried, shrunk, ground, and sieved, and kept in an oven at 105-110°C for 2-2.5 hours to obtain a dry base sample. Chemical method, in a muffle furnace controlled by a program, burn the sample at a temperature of (815±10)°C until the quality is constant to obtain ash samples, and analyze the ash components of the ash samples, and the ash component analysis uses AXIOSadvanced wavelength dispersive X-rays Fluorescence spectrometer, the results of each mineral component of the ash component analysis are shown in the following table:
[0031] Table 2 Contents of mineral components
[0032]
[0033] From Table 2, in the mixed samples obtained from A and C, the mineral components CaO, Al 2 o 3 and SiO 2 The contents accounted for 42.98%, 37.21% and 68.75% of the mixed sample respectively, it can be considered that CaO-Al 2 o 3 -SiO 2 The component system is the main component; select CaO-Al through the ternary phase diagram tool book 2 ...
Embodiment 3
[0036] Coal A and sludge sample D were dried, shrunk, ground, and sieved, and kept in an oven at 105-110°C for 2-2.5 hours to obtain dry base samples. Chemical method, in a muffle furnace controlled by a program, burn the sample at a temperature of (815±10)°C until the quality is constant to obtain ash samples, and analyze the ash components of the ash samples, and the ash component analysis uses AXIOSadvanced wavelength dispersive X-rays Fluorescence spectrometer, the results of each mineral component of the ash component analysis are shown in the following table:
[0037] Table 3 Contents of mineral components
[0038]
[0039]From Table 3, in the mixed sample obtained from coal A and sludge D, the mineral composition Fe 2 o 3 、Al 2 o 3 and SiO 2 The content accounted for 11.57%, 55.07% and 97.42% of the mixed sample respectively, it can be considered that Fe 2 o 3 -Al 2 o 3 -SiO 2 The component system is the main component; select Fe through the ternary phase d...
PUM
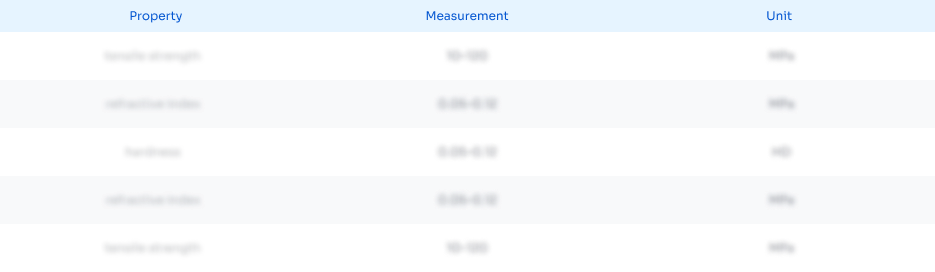
Abstract
Description
Claims
Application Information

- R&D
- Intellectual Property
- Life Sciences
- Materials
- Tech Scout
- Unparalleled Data Quality
- Higher Quality Content
- 60% Fewer Hallucinations
Browse by: Latest US Patents, China's latest patents, Technical Efficacy Thesaurus, Application Domain, Technology Topic, Popular Technical Reports.
© 2025 PatSnap. All rights reserved.Legal|Privacy policy|Modern Slavery Act Transparency Statement|Sitemap|About US| Contact US: help@patsnap.com