Z-pin reinforced composite wind turbine blade and manufacturing method thereof
A technology for reinforcing composite materials and wind turbine blades, which is applied in the field of composite material reinforcement and can solve problems such as poor connection interface performance
- Summary
- Abstract
- Description
- Claims
- Application Information
AI Technical Summary
Problems solved by technology
Method used
Image
Examples
no. 1 example
[0038] The first embodiment: as Figures 2 to 4 as shown,
[0039] The manufacturing method of Z-pin reinforced composite material wind power blade comprises the following steps:
[0040] Step 1. Prepare high-performance Z-pin4 by pultrusion process, implant Z-pin4 into foam carrier 5 according to preset Z-pin4 parameters, and make foam preform containing Z-pin;
[0041] Step 2, preparing the composite material connecting layer 3 with prepreg;
[0042] Step 3: Cover the upper half-shell 1a and the lower half-shell 1b with prepreg in the wind turbine blade mold, and place the prepreg connecting layer along the inner edge of the lower half-shell 1b, so that the prepreg connecting layer The lower half is close to the inner side of the lower half-shell 1b, and the upper half of the connecting layer 3 is located outside the lower half-shell 1b;
[0043] Step 4. Use hot pressing to bend the foam prefabricated body containing the Z-pin so that it fits the lower half of the connect...
no. 2 example
[0051] The second embodiment: as Figure 2 to Figure 4 as shown,
[0052] The manufacturing method of Z-pin reinforced composite material wind power blade comprises the following steps:
[0053]Step 1. Prepare high-performance Z-pin4 by pultrusion process, implant Z-pin4 into foam carrier 5 according to preset Z-pin4 parameters, and make foam preform containing Z-pin;
[0054] Step 2, preparing the composite material connecting layer 3 with fiber cloth;
[0055] Step 3: Cover the upper half shell 1a and the lower half shell 1b with fiber cloth in the wind power blade mold, place the fiber cloth connecting layer along the inner edge of the lower half shell 1b, so that the lower half of the fiber cloth connecting layer Close to the inner side of the lower half-shell 1b, the upper half of the connecting layer 3 is located outside the lower half-shell 1b;
[0056] Step 4. Use hot pressing to bend the foam prefabricated body containing the Z-pin so that it fits the lower half of...
PUM
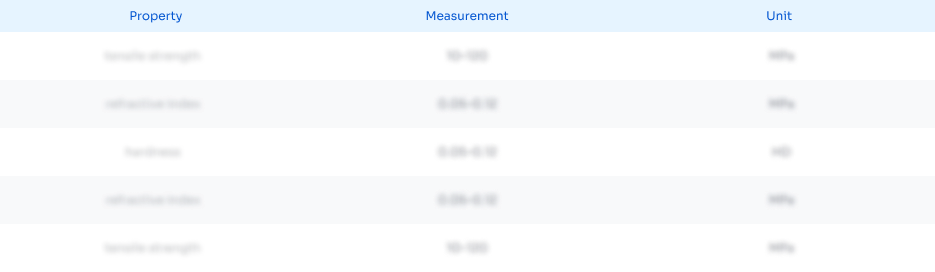
Abstract
Description
Claims
Application Information

- R&D
- Intellectual Property
- Life Sciences
- Materials
- Tech Scout
- Unparalleled Data Quality
- Higher Quality Content
- 60% Fewer Hallucinations
Browse by: Latest US Patents, China's latest patents, Technical Efficacy Thesaurus, Application Domain, Technology Topic, Popular Technical Reports.
© 2025 PatSnap. All rights reserved.Legal|Privacy policy|Modern Slavery Act Transparency Statement|Sitemap|About US| Contact US: help@patsnap.com