Denitration catalyst end part hardening liquid as well as preparation method and application thereof
A denitrification catalyst and hardening solution technology, applied in catalyst protection, chemical instruments and methods, physical/chemical process catalysts, etc., can solve the problem of aluminum sulfate not being resistant to high temperature, high price of ammonium metavanadate, adverse effects on the environment and human health And other problems, to achieve the effect of increased strength, high bond strength, and low price
- Summary
- Abstract
- Description
- Claims
- Application Information
AI Technical Summary
Problems solved by technology
Method used
Examples
Embodiment 1
[0021] First take 34g of sodium silicate and add it to 53g of water. After the sodium silicate is dissolved, add 8g of zinc oxide to it, stir for 0.5 hours, then add 5g of copper nitrate and stir for 1 hour to form a hardening solution.
[0022] After soaking the end of the honeycomb denitration catalyst in the hardening solution for 3 minutes, blow off the excess hardening solution at the end of the catalyst with compressed air; put the catalyst soaked in the hardening solution at room temperature to naturally solidify, and then program the temperature to 550 After 4 hours of calcination at °C, hardening is complete.
Embodiment 2
[0024] First take 30g of sodium silicate and add it to 58g of water. After the sodium silicate is dissolved, add 7g of zinc oxide to it, stir for 0.5 hours, then add 5g of ferrous nitrate and stir for 1 hour to form a hardening solution.
[0025] After soaking the end of the honeycomb denitration catalyst in the hardening solution for 3 minutes, blow off the excess hardening solution at the end of the catalyst with compressed air; put the catalyst soaked in the hardening solution at room temperature to naturally solidify, and then heat it up to 500 After 6 hours of calcination at ℃, hardening is complete.
Embodiment 3
[0027] First, take 26g of sodium silicate and add it to 63g of water. After the sodium silicate is dissolved, add 4g of zinc oxide to it, stir for 0.5 hours, then add 3g of copper nitrate and 4g of ferrous nitrate and stir for 2 hours to form a hardening solution. .
[0028] After soaking the end of the honeycomb denitration catalyst in the hardening solution for 5 minutes, blow off the excess hardening solution at the end of the catalyst with compressed air; put the catalyst soaked in the hardening solution at room temperature to naturally solidify, and then program the temperature to 550 After 4 hours of calcination at °C, hardening is complete.
PUM
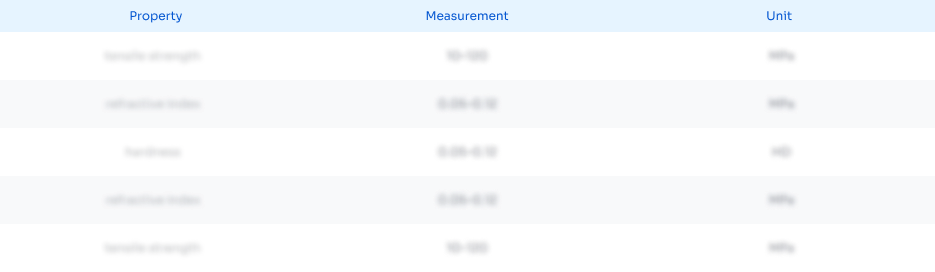
Abstract
Description
Claims
Application Information

- R&D Engineer
- R&D Manager
- IP Professional
- Industry Leading Data Capabilities
- Powerful AI technology
- Patent DNA Extraction
Browse by: Latest US Patents, China's latest patents, Technical Efficacy Thesaurus, Application Domain, Technology Topic, Popular Technical Reports.
© 2024 PatSnap. All rights reserved.Legal|Privacy policy|Modern Slavery Act Transparency Statement|Sitemap|About US| Contact US: help@patsnap.com