Vinyl acetate catalyst and application thereof
A vinyl acetate and catalyst technology, applied in the field of vinyl acetate synthesis, can solve the problems of low activity and selectivity of allyl acetate catalyst
- Summary
- Abstract
- Description
- Claims
- Application Information
AI Technical Summary
Problems solved by technology
Method used
Image
Examples
Embodiment 1
[0027] Preparation of modified carrier: Mix 0.80g of magnesium hydroxide powder with 1.0g of silica sol to obtain a coating solution, and spray the coating solution evenly on 1.1L of spherical SiO with a diameter of 5.6mm 2 on the carrier, dried at 100°C, and calcined in a muffle furnace at 500°C to obtain a carrier (X) coated with modified metal elements.
[0028] Preparation of catalyst: use sodium bicarbonate pH regulator and water as solvent to prepare pH 1.09, containing 4.23gPd and 2.05gAu chloropalladic acid, chloroauric acid aqueous solution to obtain 500ml of impregnating solution, which is immersed in the The catalyst precursor I is obtained on the support (X). After drying at 80°C, 105ml contains 22.5g Na 2 SiO 3 9H 2 The solution of O was fully mixed and aged for 24 hours to obtain the catalyst precursor II. Then use a solubility of 12% (in N 2 h 4 ·H 2 (2 in weight ratio) was reduced with 500ml of hydrazine hydrate, washed with water until there was no chl...
Embodiment 2
[0046] Preparation of modified carrier: Mix 0.40g of barium hydroxide powder with 1.0g of silica sol to obtain a coating solution, and spray the coating solution evenly on 1.1L of spherical SiO with a diameter of 5.6mm 2 on the carrier, dried at 100°C, and calcined in a muffle furnace at 500°C to obtain a carrier (X) coated with modified metal elements.
[0047] Preparation of catalyst: use sodium bicarbonate pH regulator and water as solvent to prepare pH 1.09, containing 4.23gPd and 2.05gAu chloropalladic acid, chloroauric acid aqueous solution to obtain 500ml of impregnating solution, which is immersed in the The catalyst precursor I is obtained on the support (X). After drying at 80°C, 105ml contains 22.5g Na 2 SiO 3 9H 2 The solution of O was fully mixed and aged for 24 hours to obtain the catalyst precursor II. Then use a solubility of 12% (in N 2 h 4 ·H 2 (2 in weight ratio) was reduced with 500ml of hydrazine hydrate, washed with water until there was no chlori...
Embodiment 3
[0050] Preparation of modified carrier: Mix 0.50g of calcium oxide powder and 1.0g of silica sol thoroughly to obtain a coating solution, and spray the coating solution evenly on 1.1L of spherical SiO with a diameter of 5.6mm 2 on the carrier, dried at 100°C, and calcined in a muffle furnace at 500°C to obtain a carrier (X) coated with modified metal elements.
[0051] Preparation of catalyst: use sodium bicarbonate pH regulator and water as solvent to prepare pH 1.09, containing 4.23gPd and 2.05gAu chloropalladic acid, chloroauric acid aqueous solution to obtain 500ml of impregnating solution, which is immersed in the The catalyst precursor I is obtained on the support (X). After drying at 80°C, 105ml contains 22.5g Na 2 SiO 3 9H 2 The solution of O was fully mixed and aged for 24 hours to obtain the catalyst precursor II. Then use a solubility of 12% (in N 2 h 4 ·H 2 (2 in weight ratio) was reduced with 500ml of hydrazine hydrate, washed with water until there was no...
PUM
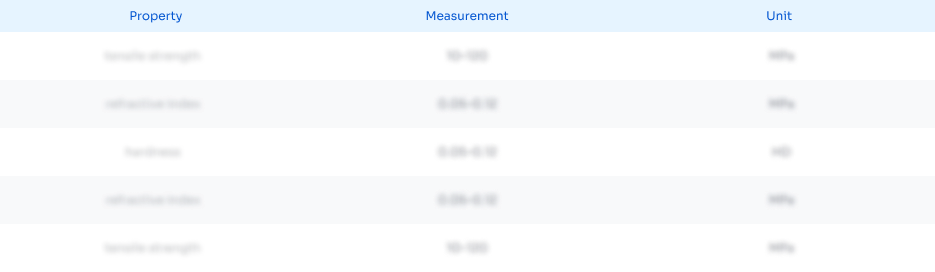
Abstract
Description
Claims
Application Information

- R&D
- Intellectual Property
- Life Sciences
- Materials
- Tech Scout
- Unparalleled Data Quality
- Higher Quality Content
- 60% Fewer Hallucinations
Browse by: Latest US Patents, China's latest patents, Technical Efficacy Thesaurus, Application Domain, Technology Topic, Popular Technical Reports.
© 2025 PatSnap. All rights reserved.Legal|Privacy policy|Modern Slavery Act Transparency Statement|Sitemap|About US| Contact US: help@patsnap.com