Preparation method of low-temperature cross-linking resin for textiles
A low-temperature cross-linking, textile technology, applied in textiles, papermaking, fiber processing, etc., can solve the problems of high energy consumption and unsatisfactory, and achieve the effect of saving energy and realizing energy saving and environmental protection.
- Summary
- Abstract
- Description
- Claims
- Application Information
AI Technical Summary
Problems solved by technology
Method used
Image
Examples
Embodiment 1
[0031] Mix 90g of vinyl acetate, 10g of acrylic acid and 10g of diacetone acrylamide to form a mixed monomer, and dissolve 0.33g of ammonium persulfate in 30g of water. Put 10g of polyvinyl alcohol 1799 and 150g of water into the reaction vessel, start stirring, raise the temperature to 90°C, keep it warm for 1.5 hours and then cool down to 75°C, then add 4.4g of sodium lauryl sulfate and isomeric tridecanol polyoxygen The composite emulsifier composed of vinyl ether, after fully dissolving, slowly add the mixed monomer and ammonium persulfate aqueous solution dropwise, and the dropwise addition is completed within 3 hours, then raise the temperature to 85°C, keep the temperature for 2 hours, cool down to below 50°C, use Adjust the pH to 7.21 with ammonia water, then add 10.3 g of adipic acid dihydrazide, stir for 1 hour, mix well and discharge, and the obtained product is a low-temperature cross-linked resin product.
[0032] See attached figure 1 , it is the infrared spectr...
Embodiment 2
[0034] Mix 90g of vinyl acetate, 10g of acrylic acid and 15g of diacetone acrylamide to form a mixed monomer, and dissolve 0.35g of ammonium persulfate in 30g of water. Put 12g of polyvinyl alcohol 1799 and 160g of water into the reaction vessel, start stirring, raise the temperature to 88°C, keep it warm for 1.5 hours and then cool down to 73°C, then add 4.6g of sodium lauryl sulfate and isomeric tridecanol polyoxygen The composite emulsifier composed of vinyl ether, after fully dissolving, slowly add the mixed monomer and ammonium persulfate aqueous solution dropwise, and the dropwise addition is completed within 3 hours, then raise the temperature to 84°C, keep the temperature for 3 hours, cool down to below 50°C, use Adjust the pH to 6.84 with ammonia water, then add 16g of adipic acid dihydrazide, stir for 1 hour, mix well and discharge, and the obtained product is a low-temperature cross-linked resin product.
[0035] See attached figure 2 , it is the infrared spectrog...
Embodiment 3
[0037] Mix 90g of vinyl acetate, 10g of methacrylic acid and 10g of diacetone acrylamide to form a mixed monomer, and dissolve 0.33g of ammonium persulfate in 30g of water. Put 10g of polyvinyl alcohol 1799 and 150g of water into the reaction vessel, start stirring, raise the temperature to 89°C, keep it warm for 1.5 hours and then cool down to 72°C, then add 4.5g of sodium lauryl sulfate and isomeric tridecanol polyoxygen The composite emulsifier composed of vinyl ether, after fully dissolving, slowly add the mixed monomer and ammonium persulfate aqueous solution dropwise, and the dropwise addition is completed within 3 hours, then raise the temperature to 83°C, keep the temperature for 2 hours, cool down to below 50°C, use Adjust the pH to 7.08 with ammonia water, then add 10.5 g of adipic acid dihydrazide, stir for 1 hour, mix well and discharge, and the obtained product is a low-temperature cross-linked resin product.
[0038] See attached image 3 , it is the infrared sp...
PUM
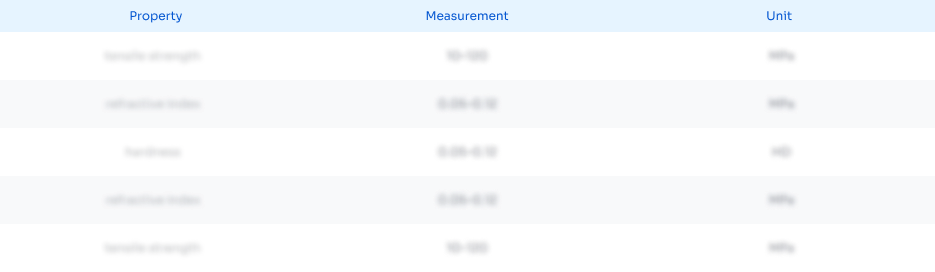
Abstract
Description
Claims
Application Information

- R&D
- Intellectual Property
- Life Sciences
- Materials
- Tech Scout
- Unparalleled Data Quality
- Higher Quality Content
- 60% Fewer Hallucinations
Browse by: Latest US Patents, China's latest patents, Technical Efficacy Thesaurus, Application Domain, Technology Topic, Popular Technical Reports.
© 2025 PatSnap. All rights reserved.Legal|Privacy policy|Modern Slavery Act Transparency Statement|Sitemap|About US| Contact US: help@patsnap.com