Fluorubber use bisphenol AF pre-dispersion mother colloidal particle formula
A pre-dispersed masterbatch and fluororubber technology, applied in the field of bisphenol AF pre-dispersed masterbatch, can solve the problems of poor dispersion and phase fusion, and achieve the effect of overcoming poor phase fusion and excellent vulcanization performance
- Summary
- Abstract
- Description
- Claims
- Application Information
AI Technical Summary
Problems solved by technology
Method used
Image
Examples
Embodiment 1
[0014] Put 4.8kg of ternary copolymerized fluororubber into the open mill to pull it through, and after 5 minutes, put it into 5kg of bisphenol AF (2,2-bis-(4-hydroxyphenyl)hexafluoropropane) powder , control the temperature of the roller at 90-110°C, after 15 minutes of mixing, add 1kg of stearic acid, 1kg of polyethylene wax and continue mixing for 5 minutes before unloading, put the material on the platform for parking, park for 3-24 hours, put it again Put the material on the open mill for mixing. At this time, the temperature of the roller is controlled between 60-80°C, and the material can be discharged after mixing for about 10 minutes. The bisphenol AF (2,2-bis-(4-hydroxyphenyl)hexafluoropropane) pre-dispersed masterbatch is obtained, and finally granulated by a single-screw extruder.
Embodiment 2
[0016] Put 3.0kg of vinylidene fluoride / ethylene fluoride and vinylidene fluoride / tetrafluoroethylene / fluoropropylene into the open mill to pull it out. After 5 minutes of thinning, put 3.5kg of bisphenol AF (2, 2-bis-(4-hydroxyphenyl)hexafluoropropane) powder, control the roller temperature at 90-110°C, knead for 15 minutes, add 0.3kg glycerol monostearate and zinc stearate, 0.1kg Ester wax and palm wax continue to mix for 5 minutes before feeding, put the material on the platform and park it for 3-24 hours, put the material on the open mill again for mixing, and control the roller temperature at 60-80°C In between, mixing for about 10 minutes can be discharged. The bisphenol AF (2,2-bis-(4-hydroxyphenyl)hexafluoropropane) pre-dispersed masterbatch is obtained, and finally granulated by a single-screw extruder.
Embodiment 3
[0018] Put 7.0kg of vinylidene fluoride / tetrafluoroethylene / metafluoropropylene fluororubber, metafluoride propylene / ethylene fluororubber and tetrafluoroethylene / propylene fluororubber into the open mill for thinning, after 5 minutes of thinning, put 5.5kg bisphenol AF (2,2-bis-(4-hydroxyphenyl) hexafluoropropane) powder, control the roll temperature at 90-110°C, knead for 15 minutes, add 3kg zinc stearate, 0.8kg Ester wax, palm wax and paraffin wax continue to be mixed for 5 minutes before feeding, put the materials on the platform for parking, park for 3-24 hours, put the materials on the open mill again for mixing, and control the temperature of the rollers at 60-80 ℃, mixing for about 10 minutes can be discharged. The bisphenol AF (2,2-bis-(4-hydroxyphenyl)hexafluoropropane) pre-dispersed masterbatch is obtained, and finally granulated by a single-screw extruder.
[0019] The bisphenol AF pre-dispersed masterbatch particle carrier fluorine rubber for the above-mentioned ...
PUM
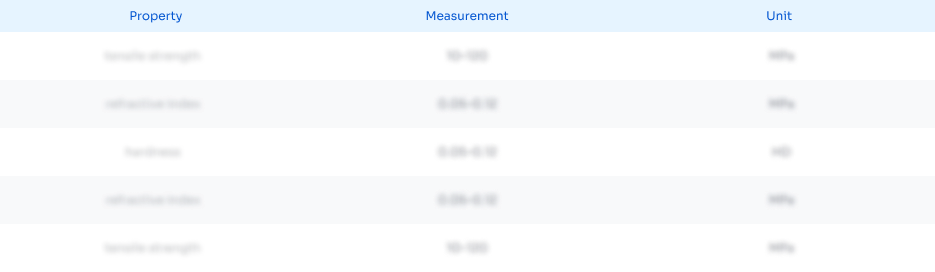
Abstract
Description
Claims
Application Information

- R&D Engineer
- R&D Manager
- IP Professional
- Industry Leading Data Capabilities
- Powerful AI technology
- Patent DNA Extraction
Browse by: Latest US Patents, China's latest patents, Technical Efficacy Thesaurus, Application Domain, Technology Topic, Popular Technical Reports.
© 2024 PatSnap. All rights reserved.Legal|Privacy policy|Modern Slavery Act Transparency Statement|Sitemap|About US| Contact US: help@patsnap.com