Synthetic method for fluororubber
A synthetic method and technology of fluororubber, applied in the field of fluororubber, can solve the problems of low Mooney value of fluororubber and inability to adapt to higher performance requirements, and achieve good vulcanization performance, good oil resistance and mild reaction conditions.
- Summary
- Abstract
- Description
- Claims
- Application Information
AI Technical Summary
Problems solved by technology
Method used
Image
Examples
Embodiment 1
[0040] The batch radical emulsion polymerization of the present invention is carried out in a 50L autoclave to prepare fluororubber. In the reactor, add 30L deionized water and 500g 5wt% ammonium perfluorooctanoate aqueous solution, 40g pH regulator disodium hydrogen phosphate, the air in the vapor space in the reactor is first replaced with nitrogen, and then replaced with mixed monomers, so that the oxygen content is less than 20ppm, the reaction kettle was raised to 120°C. Add the above-mentioned monomer mixture into the reaction kettle with a diaphragm compressor to raise the pressure to 3.5Mpa. After reaching 3.5Mpa, the reactor pressure controller is set to automatically operate at 3.5Mpa.
[0041] When the pressure of the reactor reached 3.5 MPa, the stirring was started, the mixed monomers in the reactor were fully mixed, and then 100 g of initiator solution (5 wt %) was added to start the reaction. During the reaction process, the pressure of the reactor was kept at...
Embodiment 2
[0047] The batch radical emulsion polymerization of the present invention is carried out in a 4000L autoclave to prepare fluororubber. In the reactor, add 2200L deionized water and 40Kg 5wt% perfluorooctanoic acid ammonium aqueous solution, 2.8Kg pH regulator disodium hydrogen phosphate, the air in the vapor space in the reactor is first replaced with nitrogen, and then replaced with mixed monomers to make the oxygen content Less than 20ppm, the reaction kettle was raised to 100°C. Add the above-mentioned monomer mixture into the reaction kettle with a diaphragm compressor to raise the pressure to 3.5Mpa. After reaching 3.5Mpa, the reactor pressure controller is set to automatically operate at 3.5Mpa.
[0048] When the pressure of the reactor reached 3.5MPa, the stirring was started, the mixed monomers in the reactor were fully mixed, and then 7Kg of initiator solution (5wt%) was added to start the reaction. During the reaction process, the pressure of the reactor was kept a...
Embodiment 3
[0054] The temperature of the polymerization reaction in Example 1 was changed to 90° C., and other conditions remained unchanged.
PUM
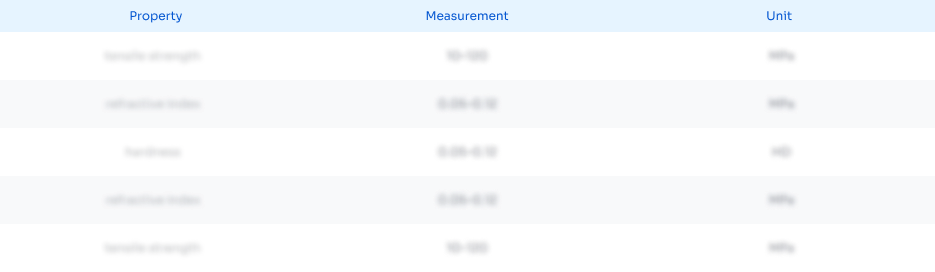
Abstract
Description
Claims
Application Information

- R&D
- Intellectual Property
- Life Sciences
- Materials
- Tech Scout
- Unparalleled Data Quality
- Higher Quality Content
- 60% Fewer Hallucinations
Browse by: Latest US Patents, China's latest patents, Technical Efficacy Thesaurus, Application Domain, Technology Topic, Popular Technical Reports.
© 2025 PatSnap. All rights reserved.Legal|Privacy policy|Modern Slavery Act Transparency Statement|Sitemap|About US| Contact US: help@patsnap.com