Low-temperature planetary high-energy bowl mill
A high-energy ball mill, planetary technology, applied in grain processing and other directions, can solve the problems of difficult operation of cooling pipes and cooling liquid circulation devices, unfavorable element alloying process, large volume of sealing devices, etc. The effect of increasing the contact area
- Summary
- Abstract
- Description
- Claims
- Application Information
AI Technical Summary
Problems solved by technology
Method used
Image
Examples
Embodiment Construction
[0021] Such as figure 1 and figure 2 As shown, the low-temperature planetary high-energy ball mill of the present invention comprises four ball mill cylinders 6 and a base 5, and each ball mill cylinder 6 is composed of an insulated tank 21, a ball mill tank 22 and a toilet bowl 17, and the ball mill tank 22 is placed in the insulated tank 21 for heat preservation. The tank 21 is placed in the toilet 17, the inner wall of the insulation tank 21 has a heat-insulating coating, the material of the ball mill tank 22 and the balls is stainless steel or zirconia or alumina; the base 5 is equipped with a revolving main shaft 9 and a frequency conversion motor 4. The frequency conversion motor 4 drives the ball mill cylinder 6 to perform planetary motion through the transmission device. The coolant main input pipe 3 connected with the liquefied gas bottle 1 extends to the opening of the liquid storage tank on the upper part of the multi-port splitter head 8, and the other ports of t...
PUM
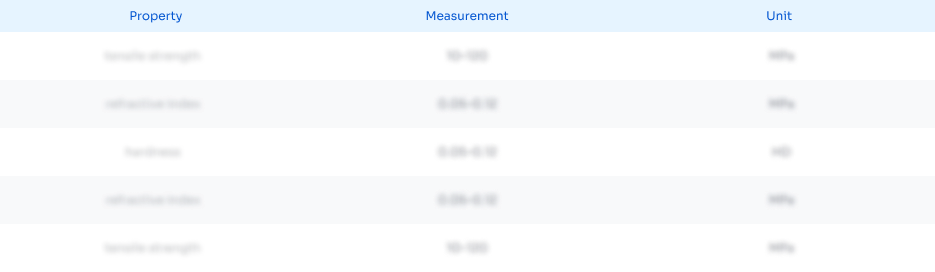
Abstract
Description
Claims
Application Information

- Generate Ideas
- Intellectual Property
- Life Sciences
- Materials
- Tech Scout
- Unparalleled Data Quality
- Higher Quality Content
- 60% Fewer Hallucinations
Browse by: Latest US Patents, China's latest patents, Technical Efficacy Thesaurus, Application Domain, Technology Topic, Popular Technical Reports.
© 2025 PatSnap. All rights reserved.Legal|Privacy policy|Modern Slavery Act Transparency Statement|Sitemap|About US| Contact US: help@patsnap.com