Surface modification method of inorganic nanoparticles as well as polytetrafluoroethylene/inorganic nanoparticle composite material
An inorganic nanoparticle, polytetrafluoroethylene technology, applied in inorganic pigment processing, chemical instruments and methods, dyeing organosilicon compound processing, etc., can solve the mechanical properties decline of composite materials, the problem of dispersion is difficult to solve, and the interface bonding force is weak. and other problems, to achieve the effect of improving mechanical properties, good macro-mechanical properties, and strong interfacial bonding force
- Summary
- Abstract
- Description
- Claims
- Application Information
AI Technical Summary
Problems solved by technology
Method used
Image
Examples
Embodiment 1
[0018] First, add 5g of nano zinc oxide and 0.2g of polyethylene glycol 400 to 100mL of deionized water, ultrasonically disperse for 1 hour to form a suspension, and then add 0.05g of lanthanum nitrate and 0.05g of disodium edetate to the suspension , sonicate at room temperature for 10 minutes, let stand for 30 minutes, then add mercaptopropyltrimethoxysilane with a mass percentage of 1 g, stir for 10 minutes, let stand for 30 minutes, centrifuge, dry, grind to obtain modified inorganic nanoparticles, and finally Blend 5g of modified inorganic nanoparticles with 95g of polytetrafluoroethylene powder, put the blended material into a stainless steel mold, and mold it with a press to obtain a green body. The molding pressure is 28MPa, and the molding time is 20min. The molded body was placed in a muffle furnace for sintering at a temperature of 350° C. and a sintering time of 2 hours. After sintering, a polytetrafluoroethylene / inorganic nanoparticle composite material was obtaine...
Embodiment 2
[0023] First, add 5 g of nano-zinc oxide and 0.2 g of polyethylene glycol 400 in 100 mL of deionized water, ultrasonically disperse for 1 h to form a suspension, and then add 0.05 g of cerium nitrate and 0.05 g of ethylenediaminetetra Disodium acetate, ultrasonic at room temperature for 10 minutes, let stand for 30 minutes, then add mercaptopropyltrimethoxysilane with a mass percentage of 1g, stir for 10 minutes, let stand for 30 minutes, centrifuge, dry, and grind to obtain modified inorganic nano Particles, finally blend 2g modified inorganic nanoparticles with 98g polytetrafluoroethylene powder, put the blended material into a stainless steel mold, and mold it with a press to obtain a green body. The molding pressure is 28MPa, and the molding time is 20min , the molded green body is placed in a muffle furnace for sintering, the sintering temperature is 350 ° C, the sintering time is 2h, and the PTFE / inorganic nanoparticle composite material is obtained after sintering.
Embodiment 3
[0025] First, add 10 g of nano-zinc oxide and 0.5 g of polyethylene glycol 400 in 100 mL of deionized water, ultrasonically disperse for 1 hour to form a suspension, and then add 0.1 g of neodymium nitrate and 0.05 g of ethylenediaminetetra Disodium acetate, sonicate for 20 minutes at room temperature, let stand for 30 minutes, then add mercaptopropyltrimethoxysilane with a mass percentage of 1.3 g, stir for 10 minutes, let stand for 30 minutes, centrifuge, dry, and grind to obtain the modified inorganic Nanoparticles, finally blend 10g modified inorganic nanoparticles with 90g polytetrafluoroethylene powder, put the blended material into a stainless steel mold, and mold it with a press to obtain a green body. The molding pressure is 28MPa, and the molding time is After 20 minutes, the molded green body was placed in a muffle furnace for sintering, the sintering temperature was 350° C., and the sintering time was 2 hours. After sintering, the polytetrafluoroethylene / inorganic n...
PUM
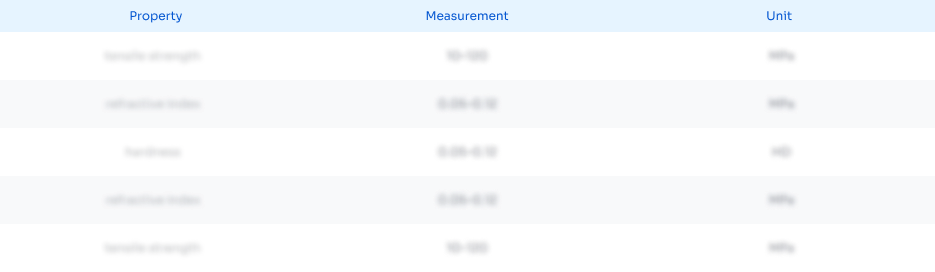
Abstract
Description
Claims
Application Information

- Generate Ideas
- Intellectual Property
- Life Sciences
- Materials
- Tech Scout
- Unparalleled Data Quality
- Higher Quality Content
- 60% Fewer Hallucinations
Browse by: Latest US Patents, China's latest patents, Technical Efficacy Thesaurus, Application Domain, Technology Topic, Popular Technical Reports.
© 2025 PatSnap. All rights reserved.Legal|Privacy policy|Modern Slavery Act Transparency Statement|Sitemap|About US| Contact US: help@patsnap.com