Prestressed wire for bridge and production process of prestressed wire
A technology of prestressed steel wire and production process, which is applied in the fields of prestressed steel wire and its production process, prestressed steel wire for bridges and its production process, and can solve a large number of problems such as manpower and material resources and economic losses, so as to improve the service life and strengthen the market. Competitiveness, the effect of ensuring stability
- Summary
- Abstract
- Description
- Claims
- Application Information
AI Technical Summary
Problems solved by technology
Method used
Examples
Embodiment 1
[0021] A prestressed steel wire for a bridge provided in this example, the chemical composition of the steel wire by weight percentage is: C: 0.45%, Si: 1.5%, Mn: 0.4%, Ni: 0.3%, Cr: 0.1%, Nb: 0.07% , Ti: 0.02%, V: 0.05%, Mo: 0.01%, P: 0.01%, S: 0.008%, composite rare earth: 0.02%, and the balance is iron and other unavoidable trace impurities; in the composite rare earth, Contains the following components by weight percentage: Ce: 12%, Sc: 15%, Gd: 11%, Pr: 15%, and the balance is La.
[0022] The prestressed steel wire production process of this embodiment includes pickling, phosphating, saponification, cold rolling, cold drawing and galvanizing processes,
[0023] (1) Pass the steel wire produced according to the above components through 15% dilute sulfuric acid for pickling, the pickling temperature is 65°C, and the pickling time is 25 minutes;
[0024] ⑵Phosphating treatment in phosphate solution, the acidity pH value is 5.5, the phosphating time is 8min, and the phospha...
Embodiment 2
[0029] A prestressed steel wire for a bridge provided in this embodiment, the chemical composition of the steel wire in weight percent is: C: 0.55%, Si: 1.9%, Mn: 1.4%, Ni: 0.5%, Cr: 0.6%, Nb: 0.21%, Ti: 0.3%, V: 0.74%, Mo: 0.03%, P: 0.012%, S: 0.009%, compound rare earth: 0.04%, the balance is iron and other unavoidable trace impurities;
[0030] The composite rare earth contains the following components by weight percentage: Ce: 14%, Sc: 19%, Gd: 15%, Pr: 20%, and the balance is La.
[0031] The prestressed steel wire production process of this embodiment includes pickling, phosphating, saponification, cold rolling, cold drawing and galvanizing processes,
[0032] (1) Pass the steel wire produced according to the above components through 20% dilute sulfuric acid for pickling, the pickling temperature is 62°C, and the pickling time is 22 minutes;
[0033] ⑵ Phosphating treatment in phosphate solution, the acidity pH value is 6.0, the phosphating time is 15min, and the phosph...
Embodiment 3
[0038] A prestressed steel wire for a bridge provided in this embodiment, the chemical composition of the steel wire in weight percentage is: C: 0.65%, Si: 2.3%, Mn: 2.2%, Ni: 0.7%, Cr: 0.8%, Nb: 0.35%, Ti: 0.6%, V: 0.1%, Mo: 0.05%, P: 0.014%, S: 0.015%, compound rare earth: 0.06%, the balance is iron and other unavoidable trace impurities;
[0039] The composite rare earth contains the following components by weight percentage: Ce: 16%, Sc: 33%, Gd: 16%, Pr: 23%, and the balance is La.
[0040] The prestressed steel wire production process of this embodiment includes pickling, phosphating, saponification, cold rolling, cold drawing and galvanizing processes,
[0041] (1) Pickling the steel wire produced according to the above components through 30% dilute sulfuric acid, the pickling temperature is 60°C, and the pickling time is 20 minutes;
[0042] ⑵ Phosphating treatment in a phosphate solution, the acidity pH value is 6.5, the phosphating time is 20min, and the phosphating...
PUM
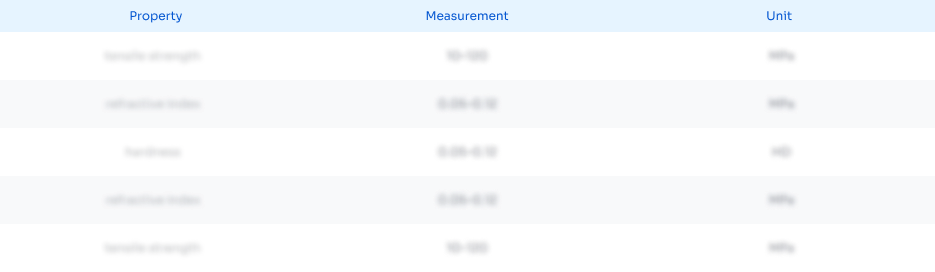
Abstract
Description
Claims
Application Information

- Generate Ideas
- Intellectual Property
- Life Sciences
- Materials
- Tech Scout
- Unparalleled Data Quality
- Higher Quality Content
- 60% Fewer Hallucinations
Browse by: Latest US Patents, China's latest patents, Technical Efficacy Thesaurus, Application Domain, Technology Topic, Popular Technical Reports.
© 2025 PatSnap. All rights reserved.Legal|Privacy policy|Modern Slavery Act Transparency Statement|Sitemap|About US| Contact US: help@patsnap.com