Preparation method of high-diffusivity water-absorbent resin
A technology of water-absorbent resin and diffusibility, which is applied in the field of preparation of highly diffusible water-absorbent resin, which can solve problems such as difficult control, complicated operation, and poor hydrophilicity of the product, and achieve the effect of increasing the contact area and improving the utilization rate
- Summary
- Abstract
- Description
- Claims
- Application Information
AI Technical Summary
Problems solved by technology
Method used
Examples
Embodiment 1
[0017] Raw material composition and the parts by weight of each composition are:
[0018] Acrylic 220
[0019] 50% sodium hydroxide solution 200
[0020] Composite crosslinking agent 5
[0021] Sodium bicarbonate 6
[0022] ethanol 22
[0023] Silica 3
[0024] Deionized water 300
[0026] Ascorbic acid 0.6
[0027] The preparation method is:
[0028] 1. Add the above-mentioned parts by weight of acrylic acid, 50% sodium hydroxide solution, composite cross-linking agent, sodium bicarbonate, ethanol, silicon dioxide and deionized water, mix well, and pass high-purity nitrogen gas to remove oxygen 20min.
[0029] 2. Add hydrogen peroxide and ascorbic acid to initiate the polymerization reaction at 5°C, and the reaction is considered to be over if the temperature does not rise any longer. The peak temperature is about 85°C, and the temperature is kept for 2 hours.
[0030] 3. Granulate the colloid and dry it at 180°C until the moisture co...
Embodiment 2
[0033] Raw material composition and the parts by weight of each composition are:
[0034] Acrylic 260
[0035] 50% sodium hydroxide solution 256
[0036] Composite crosslinking agent 7
[0037] Sodium bicarbonate 8
[0038] ethanol 36
[0039] Silica 5
[0040] Deionized water 400
[0042] Ascorbic acid 0.7
[0043] The preparation method is:
[0044] 1. Add the above-mentioned parts by weight of acrylic acid, 50% sodium hydroxide solution, composite cross-linking agent, sodium bicarbonate, ethanol, silicon dioxide and deionized water, mix well, and pass high-purity nitrogen gas to remove oxygen 20min.
[0045] 2. Add hydrogen peroxide and ascorbic acid to initiate the polymerization reaction at 6°C, and the reaction is considered to be over if the temperature does not rise any longer. The peak temperature is 90°C, and the temperature is kept for 2 hours.
[0046] 3. Granulate the colloid and dry it at 180°C until the moisture content is...
Embodiment 3
[0049] Raw material composition and the parts by weight of each composition are:
[0050] Acrylic 300
[0051] 50% sodium hydroxide solution 300
[0052] Composite crosslinking agent 10
[0053] Sodium bicarbonate 10
[0054] ethanol 50
[0055] Silica 6
[0056] Deionized water 500
[0057] Hydrogen peroxide 1.2
[0058] Ascorbic acid 0.7
[0059] The preparation method is:
[0060] 1. Add the above-mentioned parts by weight of acrylic acid, 50% sodium hydroxide solution, composite cross-linking agent, sodium bicarbonate, ethanol, silicon dioxide and deionized water, mix well, and pass high-purity nitrogen gas to remove oxygen 20min.
[0061] 2. Add hydrogen peroxide and ascorbic acid to initiate the polymerization reaction at 6°C, and the reaction is considered to be over if the temperature does not rise any longer. The peak temperature is about 90°C, and the temperature is kept above 80°C for 2 hours.
[0062] 3. Granulate the colloid and dry it at 180°C until th...
PUM
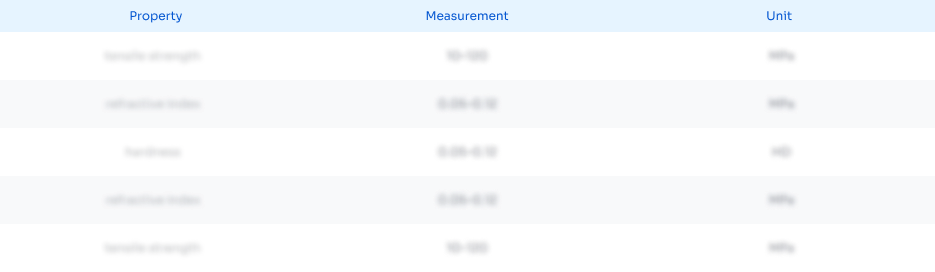
Abstract
Description
Claims
Application Information

- R&D
- Intellectual Property
- Life Sciences
- Materials
- Tech Scout
- Unparalleled Data Quality
- Higher Quality Content
- 60% Fewer Hallucinations
Browse by: Latest US Patents, China's latest patents, Technical Efficacy Thesaurus, Application Domain, Technology Topic, Popular Technical Reports.
© 2025 PatSnap. All rights reserved.Legal|Privacy policy|Modern Slavery Act Transparency Statement|Sitemap|About US| Contact US: help@patsnap.com