Preparation method of high-performance epoxy resin composition for LED (light-emitting diode) packaging
A technology of LED packaging and epoxy resin, applied in electrical components, circuits, semiconductor devices, etc., can solve the problems of reducing the glass transition temperature of materials, affecting the performance of materials, increasing the crosslinking density of finished products, etc., to enhance the resistance to yellowing. and UV resistance, increase the glass transition temperature, and improve the effect of brittleness
- Summary
- Abstract
- Description
- Claims
- Application Information
AI Technical Summary
Problems solved by technology
Method used
Image
Examples
Embodiment 1
[0035] In the preparation of epoxy resin mixture raw materials, the preparation method of polyurethane modified epoxy resin A is as follows:
[0036] ①Put 200g of PPG1000 polyether polyol into the reaction kettle, dehydrate at 100-110°C and -0.95MPa for 2-3 hours until the moisture is less than 0.05%, then cool down to 70-100°C, and pour it into the reaction kettle 69.6g of TDI was put in and reacted for 2-3 hours to obtain an isocyanate-terminated prepolymer.
[0037] ②Dehydrate 375.6.0g of E-44 epoxy resin at 100-110°C and below -0.95MPa for 2-3 hours until the water content is less than 0.05%, then cool down to 70-90°C, and add 200g of E-44 epoxy resin under nitrogen protection After reacting the isocyanate-terminated prepolymer for 2-3 hours, add 3.7g of dibutyltin dilaurate as a catalyst, and continue the reaction for 0.5-1.0 hours to obtain polyurethane-modified epoxy resin A with a predetermined structure.
[0038] The experimental formula is as follows:
[0039]
...
Embodiment 2
[0046] In the preparation of epoxy resin mixture raw materials, the preparation method of polyurethane modified epoxy resin B is as follows:
[0047] ①Put a certain amount of 100g of PPG1000 and 50g of PPG3000 polyether polyol into the reaction kettle, dehydrate at 100-110°C and below -0.95MPa for 2-3 hours until the moisture is less than 0.05%, and then cool down to 70- At 100°C, 51.8g of IPDI was put into the reactor, and after 2-3 hours of reaction, an isocyanate-terminated prepolymer was obtained.
[0048] ② Dehydrate 422.8g of E-51 epoxy resin at 100-110°C and -0.95MPa for 2-3 hours until the water content is less than 0.05%, then cool down to 70-90°C, and add 160g of epoxy resin under nitrogen protection. After reacting the isocyanate prepolymer for 2-3 hours, add 4.2g of dibutyltin dilaurate as a catalyst, and continue the reaction for 0.5-1.0 hours to obtain polyurethane-modified epoxy resin B with a predetermined structure.
[0049] The experimental formula is as fol...
Embodiment 3
[0056] In the preparation of epoxy resin mixture raw materials, the preparation method of polyurethane modified epoxy resin C is as follows:
[0057] ①Put 150g of CMA-2270 polyester polyol into the reaction kettle, dehydrate at 100-110°C and below -0.95MPa for 2-3 hours until the moisture is less than 0.05%, and then cool down to 70-100°C, to the reaction 25.2 g of HDI was put into the kettle, and after 2-3 hours of reaction, an isocyanate-terminated prepolymer was obtained.
[0058] ②Dehydrate 173.5g of E-44 epoxy resin at 100-110°C and below -0.95MPa for 2-3 hours until the water content is less than 0.05%, then cool down to 70-90°C, and add 160g of epoxy resin under nitrogen protection After reacting the isocyanate prepolymer for 2-3 hours, add 1.7g of dibutyltin dilaurate as a catalyst, and continue the reaction for 0.5-1.0 hours to obtain polyurethane-modified epoxy resin C with a predetermined structure.
[0059] The experimental formula is as follows:
[0060]
[0...
PUM
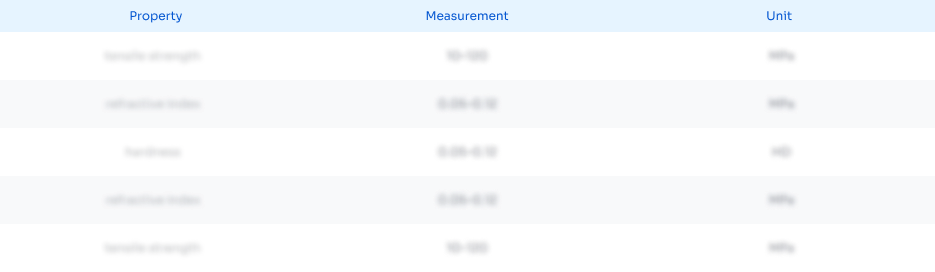
Abstract
Description
Claims
Application Information

- R&D
- Intellectual Property
- Life Sciences
- Materials
- Tech Scout
- Unparalleled Data Quality
- Higher Quality Content
- 60% Fewer Hallucinations
Browse by: Latest US Patents, China's latest patents, Technical Efficacy Thesaurus, Application Domain, Technology Topic, Popular Technical Reports.
© 2025 PatSnap. All rights reserved.Legal|Privacy policy|Modern Slavery Act Transparency Statement|Sitemap|About US| Contact US: help@patsnap.com