Grinding wheel dressing method and device for machining bearing inner ring raceway crowning
A technology of grinding wheel dressing and raceway convexity, which is applied in the field of mechanical processing, can solve the problems of high precision, failure to meet precision requirements, and complex structure of mechanical transmission devices, and achieve superior economy, high overload capacity, and simple maintenance Effect
- Summary
- Abstract
- Description
- Claims
- Application Information
AI Technical Summary
Problems solved by technology
Method used
Image
Examples
Embodiment 1
[0043] Such as figure 2 As shown, the grinding wheel dressing method for processing the convexity of the bearing inner ring raceway of the present invention firstly rotates the grinding wheel 7 in the Y and Z axis spaces, makes the outer circle generatrix of the grinding wheel parallel to the X axis space, and then puts the diamond pen 8. The reciprocating swing in the Y-axis space acts as a circular arc movement, and the diamond pen trims the outer circle of the grinding wheel during the movement to form a new concave hyperbolic generatrix of the outer circle.
[0044] Specific steps are as follows:
[0045] 1. Adjustment process.
[0046] 1.1. Drive the grinding wheel seat carriage 10 to move to the right, and the grinding wheel is more than 3mm away from the diamond pen.
[0047] 1.2. Adjust the radius of arc rotation and the distance from the center of diamond pen 8 to the center of drive shaft 9 according to the convexity requirements.
[0048] 1.3. Rotate the diamon...
Embodiment 2
[0068] Such as Figures 3 to 5 As shown, the trimming device realized according to the trimming method described in Embodiment 1 of the present invention includes a machine tool base 1, a trimmer base 2 is installed on one side of the machine tool base 1, and a worm gear reducer is installed on the trimmer base 2 3, the arc-shaped rotating rocker 6 is installed on the rotating shaft 9 of the worm gear reducer 3, and the diamond pen 8 is installed on the arc-shaped rotating rocker 6, and the diamond pen 8 is limited by the positioning switch 4; 5 Within the range, it can reciprocate and swing in a circular arc motion. The other side of the machine tool base 1 is equipped with a grinding wheel base carriage 10, and a grinding wheel 7 is installed on the grinding wheel base carriage 10. The grinding wheel 7 is driven by a motor to rotate. The grinding wheel seat carriage 10 can move left and right on the machine tool base 1, specifically in a jogging manner. The trimmer base 2 i...
PUM
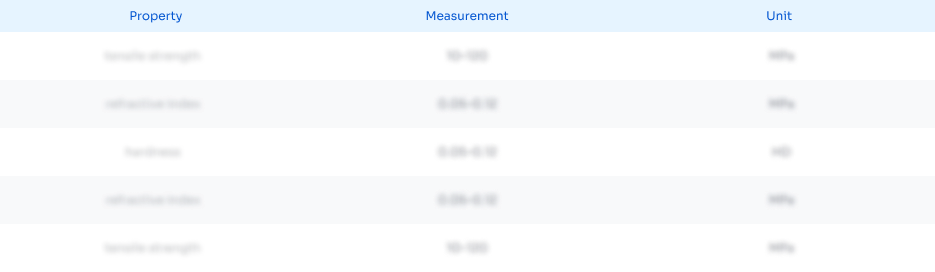
Abstract
Description
Claims
Application Information

- R&D
- Intellectual Property
- Life Sciences
- Materials
- Tech Scout
- Unparalleled Data Quality
- Higher Quality Content
- 60% Fewer Hallucinations
Browse by: Latest US Patents, China's latest patents, Technical Efficacy Thesaurus, Application Domain, Technology Topic, Popular Technical Reports.
© 2025 PatSnap. All rights reserved.Legal|Privacy policy|Modern Slavery Act Transparency Statement|Sitemap|About US| Contact US: help@patsnap.com