Deburring method for amorphous alloy
An amorphous alloy and deburring technology, which is used in metal processing equipment, resistance welding equipment, manufacturing tools, etc., can solve the problem of crystallization of amorphous alloys with short production time and deburring effect, and avoid oxidation reaction and crystallization. The effect of low reaction, equipment cost and short production time
- Summary
- Abstract
- Description
- Claims
- Application Information
AI Technical Summary
Problems solved by technology
Method used
Image
Examples
Embodiment 1
[0038] See figure 1 and Figure 4 . A method for deburring amorphous alloys in this embodiment uses the electrode 1 to release the 100J electric energy stored in the capacitor 2, and uses the electric energy released by the electrode 1 for the 1×10 -6 The burr part of the amorphous alloy 3 is heated to the glass transition temperature Tg and the melting temperature T within a second of heating time 1 After that, use the electrode 1 as a punch to apply a pressure of 15 MPa to the burr part of the amorphous alloy 3 to remove the burr, and blow nitrogen gas with a pressure of 0.1 Pa to the burr part to achieve the purpose of cooling while removing the burr. Wherein, in the whole process of removing burrs, the crystallization reaction of the amorphous alloy 3 is prevented from taking place based on the TTT diagram. Wherein, the end of the electrode 1 in contact with the burr portion of the amorphous alloy 3 is set as the tip portion 11 , so that the burr can be easily removed....
Embodiment 2
[0041] See figure 1 and Figure 4 . A method for deburring amorphous alloys in this embodiment uses the electrode 1 to release the 1000J electric energy stored in the capacitor 2, and uses the electric energy released by the electrode 1 in a 1×10 -5 The burr part of the amorphous alloy 3 is heated to the melting temperature T in a heating time of 2 seconds 1 The burrs are melted above, and then argon gas with a pressure of 5 Pa is blown to the burrs to achieve the purpose of blowing away the burrs and cooling them. Wherein, in the whole process of removing burrs, the crystallization reaction of the amorphous alloy 3 is prevented from taking place based on the TTT diagram. Wherein, the end of the electrode 1 in contact with the burr portion of the amorphous alloy 3 is set as the tip portion 11 , so that the burr can be easily removed.
[0042] The method for deburring an amorphous alloy in Example 2 has the advantages of short production time, low production cost, and good...
Embodiment 3
[0044] See figure 1 and Figure 4 . A method for deburring amorphous alloys in this embodiment uses the electrode 1 to release the 10000J electric energy stored in the capacitor 2, and uses the electric energy released by the electrode 1 in a 1×10 -4 The burr part of the amorphous alloy 3 is heated to the glass transition temperature Tg and the melting temperature T within a second of heating time 1 After the interval, use the electrode 1 as a punch to apply a pressure of 30 MPa to the burr of the amorphous alloy 3 to remove the burr. While removing the burr, helium with a pressure of 0.5 Pa is used to blow the burr to achieve the purpose of cooling. Wherein, in the whole process of removing burrs, the crystallization reaction of the amorphous alloy 3 is prevented from taking place based on the TTT diagram. Wherein, the end of the electrode 1 in contact with the burr portion of the amorphous alloy 3 is set as the tip portion 11 , so that the burr can be easily removed.
...
PUM
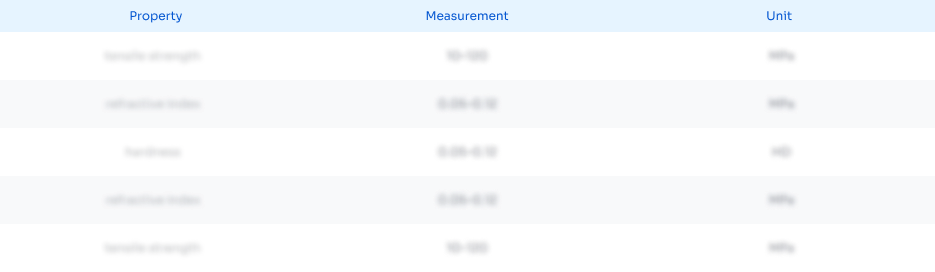
Abstract
Description
Claims
Application Information

- R&D
- Intellectual Property
- Life Sciences
- Materials
- Tech Scout
- Unparalleled Data Quality
- Higher Quality Content
- 60% Fewer Hallucinations
Browse by: Latest US Patents, China's latest patents, Technical Efficacy Thesaurus, Application Domain, Technology Topic, Popular Technical Reports.
© 2025 PatSnap. All rights reserved.Legal|Privacy policy|Modern Slavery Act Transparency Statement|Sitemap|About US| Contact US: help@patsnap.com