Preparation method of high-yield biochar
A biochar, high-yield technology, used in biofuels, educts, special forms of dry distillation, etc., can solve the problems of high temperature of 105 ° C and long immersion time, and achieve high yield, wide application range, and reduced volatility. The effect of the generation of matter
- Summary
- Abstract
- Description
- Claims
- Application Information
AI Technical Summary
Problems solved by technology
Method used
Examples
Embodiment 1
[0023] Put the collected rice stalks into an aqueous solution containing 0.5% by weight of boric acid, the weight of the rice stalks is 5% of the weight of the whole system, stir and soak at room temperature for 1 hour, and filter out the liquid with a filter screen to obtain 0.5wt% boric acid, water by weight 50% rice straw, the rice straw on the filter screen was transferred to the pyrolysis furnace, under the protective atmosphere of high-purity nitrogen, the heating rate was raised to 100°C at a rate of 0.5°C / min, kept for 1 hour, and then Raise the temperature at a rate of 0.5 °C / min to 240 °C, keep the temperature for 1 hour, and finally raise the temperature at a rate of 10 °C / min to 500 °C, keep the temperature for 1 hour, and cool with the furnace to obtain biochar with a yield of 55 wt%.
Embodiment 2
[0025] Put the collected rice husks into an aqueous solution containing 10% by weight of potassium permanganate, the weight of the rice husks is 20% of the weight of the whole system, stir and soak at room temperature for 5 hours, and filter out the liquid with a filter screen to obtain potassium permanganate-containing 5wt% rice husk with a weight moisture content of 150%, the rice husk on the filter screen is transferred to the pyrolysis furnace, under the protective atmosphere of high-purity argon, the temperature rises to 180°C at a rate of 2°C / min, and the temperature is kept for 2 hours, then raised to 300°C at a heating rate of 3°C / min, kept for 3 hours, and finally raised to 900°C at a heating rate of 50°C / min, kept at a temperature of 4 hours, and then cooled with the furnace to obtain biochar, with a yield of 40.1 wt%.
Embodiment 3
[0027] Put the collected bamboo into a solution containing 5% by weight of γ-aminopropyltriethoxysilane, the weight of the bamboo is 10% of the weight of the whole system, stir and soak at room temperature for 5 hours, and filter the liquid with a filter screen to obtain γ-aminopropyltriethoxysilane 1wt%, the bamboo material of weight moisture content 80%, the bamboo material on the filter screen is transferred in the pyrolysis furnace, under the atmosphere that nitrogen and water vapor volume ratio are 90:10, with 2 The heating rate of ℃ / min was raised to 180°C, kept for 2 hours, then raised to 300°C at a rate of 3°C / min, kept for 3 hours, and finally raised to 900°C at a rate of 50°C / min, kept for 4 hours Hours, the biochar is obtained with furnace cooling, and the yield is 49wt%.
PUM
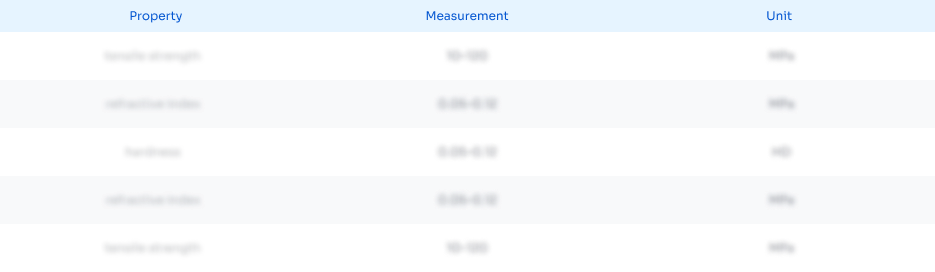
Abstract
Description
Claims
Application Information

- R&D
- Intellectual Property
- Life Sciences
- Materials
- Tech Scout
- Unparalleled Data Quality
- Higher Quality Content
- 60% Fewer Hallucinations
Browse by: Latest US Patents, China's latest patents, Technical Efficacy Thesaurus, Application Domain, Technology Topic, Popular Technical Reports.
© 2025 PatSnap. All rights reserved.Legal|Privacy policy|Modern Slavery Act Transparency Statement|Sitemap|About US| Contact US: help@patsnap.com