Method for preparing laminated conductive titanium-aluminum-carbon honeycomb ceramic by using element powder in situ and application
A honeycomb ceramic, in-situ preparation technology, applied in chemical instruments and methods, catalyst carriers, physical/chemical process catalysts, etc., can solve problems such as collapse, large closed pores, product deformation, etc., to achieve low production costs and overcome high costs. , the effect of reducing production costs
- Summary
- Abstract
- Description
- Claims
- Application Information
AI Technical Summary
Problems solved by technology
Method used
Image
Examples
Embodiment 1
[0033]Using absolute ethanol as the medium, Ti powder (325 mesh), Al powder (10 μm), graphite powder (1 μm) and binder dextrin (accounting for 8% of the weight of the ceramic powder) are mixed in molar ratio Ti: Al: C The ratio of 2:1.48:1 is mixed, wet mixed in a polyurethane ball mill tank, the volume ratio of the mixed material to absolute ethanol is 3:2, the weight ratio of the ball to material is 1.5, and the wet mixing time is 8 hours. After the mixed powder is dried, add a solution made of plasticizer glycerin and deionized water for kneading. The amount of deionized water added is 13% of the weight of the ceramic powder, and the amount of glycerin added is 2% of the weight of the ceramic powder. . Lubricant edible oil is added, and kneading is continued to finally obtain a ceramic mud body, and the amount of the lubricant added is 0.8% of the weight of the ceramic powder. After aging for 12 hours, use a single cross-section of 30×30mm 2 , It can extrude 200 through t...
Embodiment 2
[0035] Using absolute ethanol as the medium, Ti powder (325 mesh particle size), Al powder (10 μm), graphite powder (1 μm) and binder starch (accounting for 5% of the weight of the ceramic powder) were mixed according to the molar ratio Ti: Al: C The ratio of 2:1.48:1 is mixed, wet mixed in an agate ball mill jar, the volume ratio of the mixture to absolute ethanol is 2:1, the weight ratio of the ball to material is 0.5, and the wet mixing time is 6 hours. After the mixed powder is dried, add a solution made of plasticizer glycerin and deionized water for mixing. The amount of deionized water added is 12% of the weight of the ceramic powder, and the amount of glycerin added is 1% of the weight of the ceramic powder. . Lubricant edible oil is added, and kneading is continued to finally obtain a ceramic mud body, and the amount of lubricant added is 0.5% of the weight of the ceramic powder. After aging for 12 hours, a single section is 30×30mm 2 , It can extrude 200 through th...
Embodiment 3
[0037] Using absolute ethanol as the medium, Ti powder (325 mesh particle size), Al powder (10 μm), graphite powder (1 μm) and binder starch (accounting for 10% of the weight of the ceramic powder) were mixed in molar ratio Ti: Al: C Mix in the ratio of 3:1.2:1.8, wet mix in an agate ball mill jar, the volume ratio of the mixture to absolute ethanol is 3:2, the weight ratio of the ball to material is 2, and the wet mixing time is 12 hours. After the mixed powder is dried, add a solution made of plasticizer glycerin and deionized water for mixing. The amount of deionized water added is 16% of the weight of the ceramic powder, and the amount of glycerin added is 3% of the weight of the ceramic powder. . Lubricant mineral oil is added, and the kneading is continued to finally obtain ceramic mud. The amount of mineral oil added is 1% of the weight of the ceramic powder. After aging for 12 hours, a single section is 30×30mm 2 , It can extrude 200 through the mold with square hole...
PUM
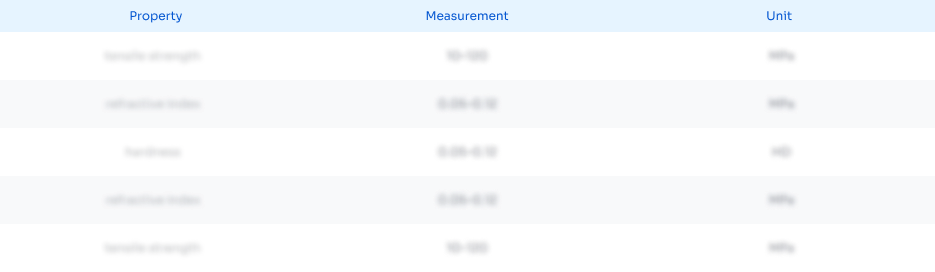
Abstract
Description
Claims
Application Information

- R&D
- Intellectual Property
- Life Sciences
- Materials
- Tech Scout
- Unparalleled Data Quality
- Higher Quality Content
- 60% Fewer Hallucinations
Browse by: Latest US Patents, China's latest patents, Technical Efficacy Thesaurus, Application Domain, Technology Topic, Popular Technical Reports.
© 2025 PatSnap. All rights reserved.Legal|Privacy policy|Modern Slavery Act Transparency Statement|Sitemap|About US| Contact US: help@patsnap.com