Iron pattern sand-lined casting process
A casting process, iron mold sand-coated technology, applied in the direction of manufacturing tools, casting molding equipment, casting molds, etc., can solve deformation, long size, uneven, the thinnest part is only 10 mm, and the thickest part can even reach 76 mm and other issues, to achieve the effect of high dimensional accuracy, small deformation, and reduced deformation
- Summary
- Abstract
- Description
- Claims
- Application Information
AI Technical Summary
Problems solved by technology
Method used
Examples
Embodiment 1
[0020] Iron mold sand-covered casting process, according to the following process:
[0021] The first step is to transfer the lower sand box and the upper sand box to the cleaning area. The upper sand box and the lower sand box are turned over by the turning machine so that the opening direction is downward, and then the upper and lower sand boxes are sent to the top perforating machine for cleaning. The molding sand in the hole will enter the vibrating shakeout machine to clean the residual sand in the cavity to complete the cleaning work. Turn the cleaned upper sand box and lower sand box through the box turning machine to the opening direction upward. After manual inspection, according to the sand The temperature of the box is adjusted. After the temperature adjustment, the upper sand box and the lower sand box are turned over and the opening direction is downward, waiting for molding;
[0022] The second step is to send the upper sand box and the lower sand box into the mo...
Embodiment 2
[0031] The difference between this example and Example 1 is that the process conditions in the fifth step are that the pouring temperature of the molten iron is 1600°C, and the pouring time is less than 60 seconds; the temperature of the molten iron is 1650°C, and the spheroidization and inoculation treatments are carried out. The high temperature of the furnace can shorten the time from the furnace to the pouring, and reduce the degree of oxidation of the molten iron by the external environment. The content of carbon in the molten iron is 4.0%, and the content of silicon is 2.5%.
Embodiment 3
[0033] The difference between this example and Example 1 is that the process conditions in the fifth step are that the pouring temperature of the molten iron is 1500°C, and the pouring time is less than 60 seconds; wherein the temperature of the molten iron is 1550°C, and the spheroidization and inoculation treatments are carried out. The high temperature of the furnace can shorten the time from the furnace to the pouring, and reduce the degree of oxidation of the molten iron by the external environment. The content of carbon in the molten iron is 3.8%, and the content of silicon is 2.3%.
PUM
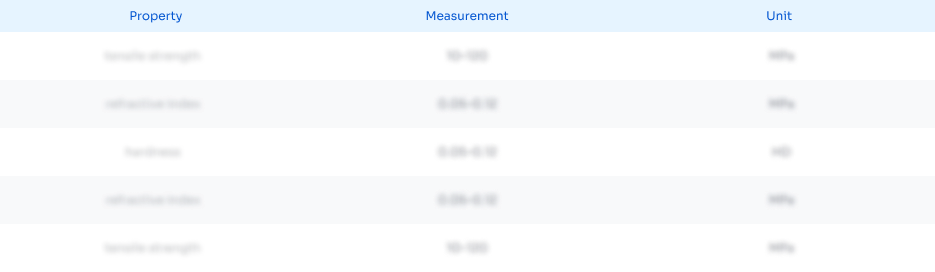
Abstract
Description
Claims
Application Information

- R&D
- Intellectual Property
- Life Sciences
- Materials
- Tech Scout
- Unparalleled Data Quality
- Higher Quality Content
- 60% Fewer Hallucinations
Browse by: Latest US Patents, China's latest patents, Technical Efficacy Thesaurus, Application Domain, Technology Topic, Popular Technical Reports.
© 2025 PatSnap. All rights reserved.Legal|Privacy policy|Modern Slavery Act Transparency Statement|Sitemap|About US| Contact US: help@patsnap.com